旧車で最も怖いのは、マシントラブルだろう。
25年くらいZ1Rに乗ってきたが、路上で自走不可能になるほどのトラブルは皆無と言っていい。
ただ、工具や技術が無かったらアウトだった、という場面もある。
自宅から何十キロも離れた場所でクラッチワイヤーが切れたとか。
北海道のど真ん中でドライブスプロケットのナットが外れたとか。
ロングツーリングに行くとなれば、それなりの準備が必要だが、旧いバイクは車載工具も貧弱で、積載スペースもほとんどない(ZRXのストレージを見た時は、かなり驚きだった)。
幸い、エアクリーナーボックスを外したのとバッテリーをリチウムにしたので、シート下のスペースは相当広くなった。
オシャレでイカしたライダーだったら、さらに電装品を目立たぬ場所に移設して「スカチューン」にするんだろうけど、あたしンちのお母さんが如く「そんなのもったいないわよー」と、そこは荷物を入れるストレージに。
バッテリーのあった場所には「パンク修理キット」。
ピッタリとおさまってくれる。
その上にソケットレンチなど小さな工具を入れた箱を置く。
さすがは「高級明太子」が入った箱、いい感じに収まってくれた。
問題はドライバー、プライヤー、ペンチなどの「ながもの」工具。
よくあるのが革製のグルグル巻きのツールケース(ツールバッグ)。
工具ひとつひとつをポケットに入れるので、多少の振動があっても工具がこぼれおちることは無い。

フレームにピッタリと合わせることを考えると「台形」がいいんだけど、都合よくそういう入れ物が見つかるハズもなく。
自作するとしても、どういうサイズ感になるのか、段ボールで「モックアップ」を制作。
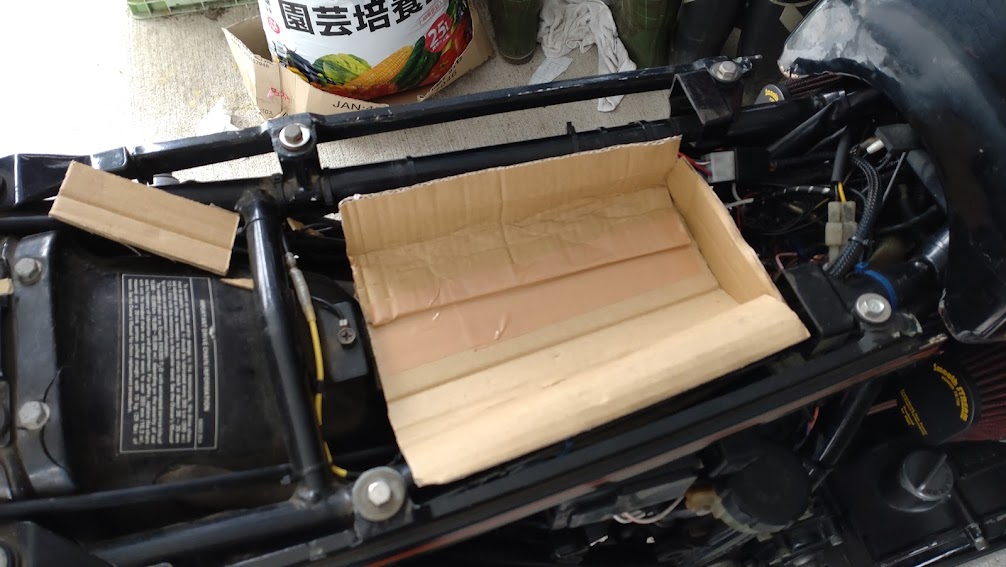
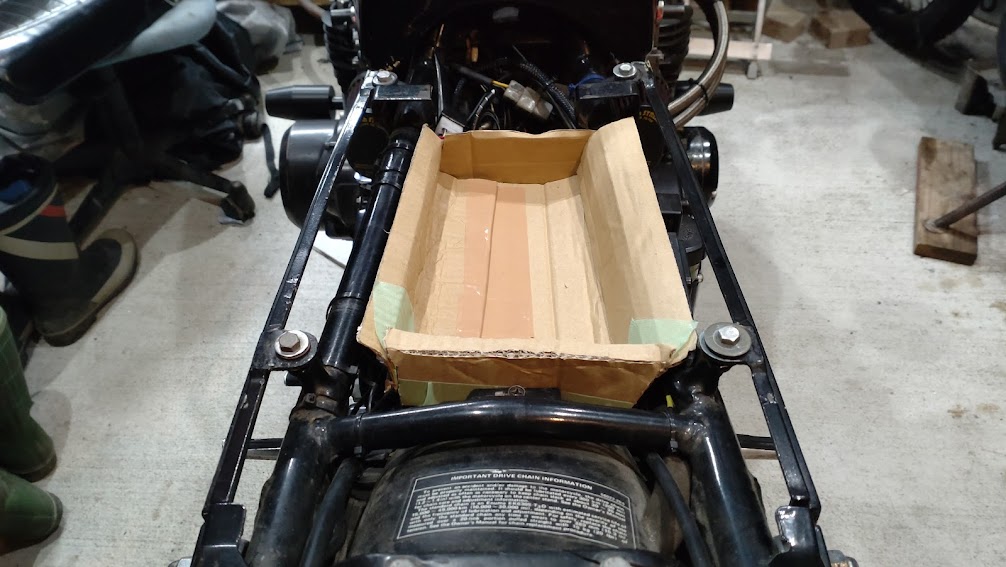
切った貼ったを繰り返して出来た「型紙」。
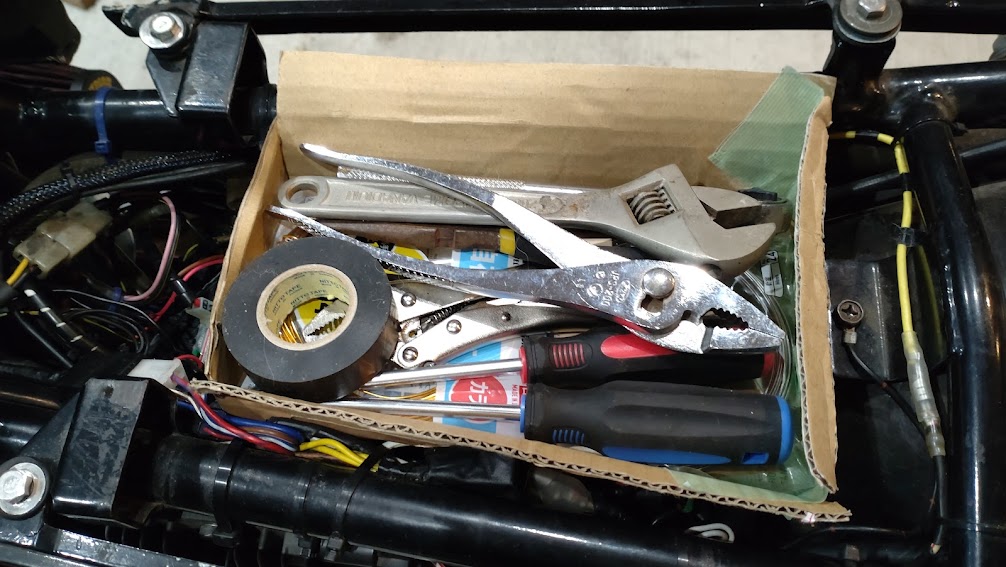
こんな感じか…としげしげと型紙を眺めること十数秒。
「…これでいいんじゃない?十分でしょ」
と、850kmツーリングにはこのまま出掛けたわけです(笑)。
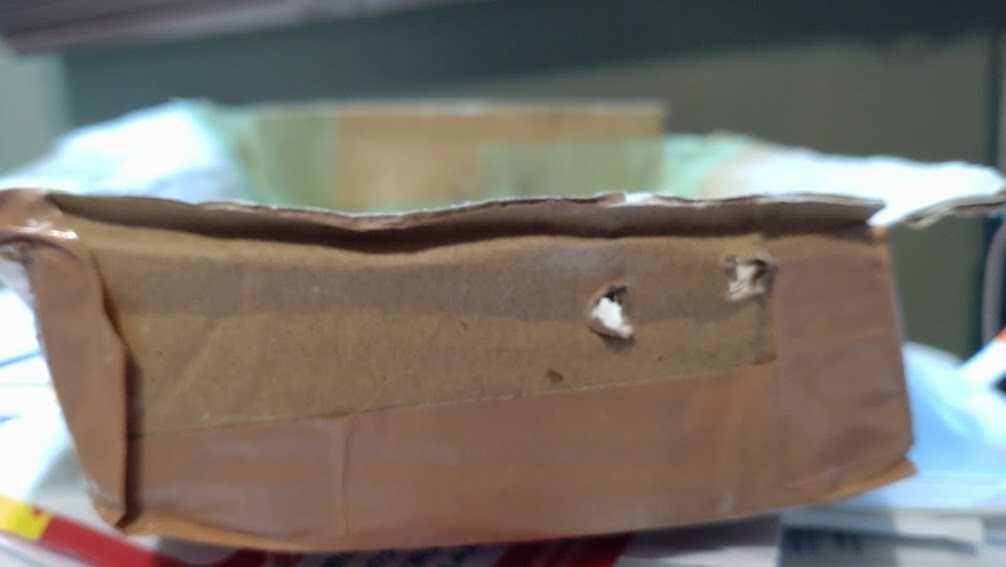
ところが、幾度となくストップアンドゴーを繰り返したせいで穴が開いたり、湿気で段ボールそのものがフニャフニャに。
アルミやステンで造ったらカッコいいのは分かる。
けど、ワンオフ製作したら、それなりにお金もかかる。
じゃあ、自分で出来るかというと、我が家のショボいハンドツールでは金属材料の切削加工は時間も手間もかかる。
工具を買えばいいかもしれないけど、この先そんなに使うだろうか?
もちろん、使用頻度は少ない。
金属がダメなら樹脂は?
もう少し精度の良い型紙をつくり、FRPで成型したらどうだろうか。
アイディアは悪くないが、FRPもそれなりに高い。
あとは木材?
個人的には「木」も何らかの形で使うのは面白いとは思っているが、さすがにここじゃない。
強度を持たせるためには、薄い板では造りづらい。
厚みを持たせたらスペースも減るし本末転倒。
やっぱり、ここは金属でしょう。
この頃は100均にも金属板が売っているのだが、必要はサイズは売っていなかった。
次に行ったのはホームセンター。
アルミ、真鍮、ステンレスなど、たくさんの素材が並んでいる。
サイズ(面積)、厚みが増えるほど、価格も倍以上となり、金額も高くなる。
金額は仕方ないとしても、あまり分厚い素材で造ろうとすると加工が大変になる。
普段、金属加工やったことのないサンメカが、ハンドツールでチャレンジしたら1mmでも厳しいんじゃないだろうか。
強度を考えれば1mmは理想的なのだが、ブラケットのように部品をマウントすることもないし、箱状に組んでしまえば大丈夫だろうというので、0.5mm厚のアルミ板を購入。
近所のカインズホームで500円しなかった。
まずは段ボールの型紙から各部の寸法を採寸。
適当に作った型紙なので、見た目からして歪んでいる。
そこは左右対称にリファインするのだけど、大事なのは出来上がりのサイズ。
シートのフレームに挟まるように置くので、それよりも幅が大きいと収まらなくなる。
目いっぱいギリギリで作るよりも数ミリ小さく作った方がよい。
それと購入したアルミ板はサイズが小さく、イメージ通りの仕上がりにならない様子。
買い直しも検討したが、とりあえず組んでみることに。
図面なしの一発勝負なので、アルミ板にマジックで線を入れる時は細心の注意を払う。
線を消すのが面倒臭くて包装用のビニールに線を入れたのだが、包装材が歪んで正しい採寸が出来なくなるのでオススメしない。
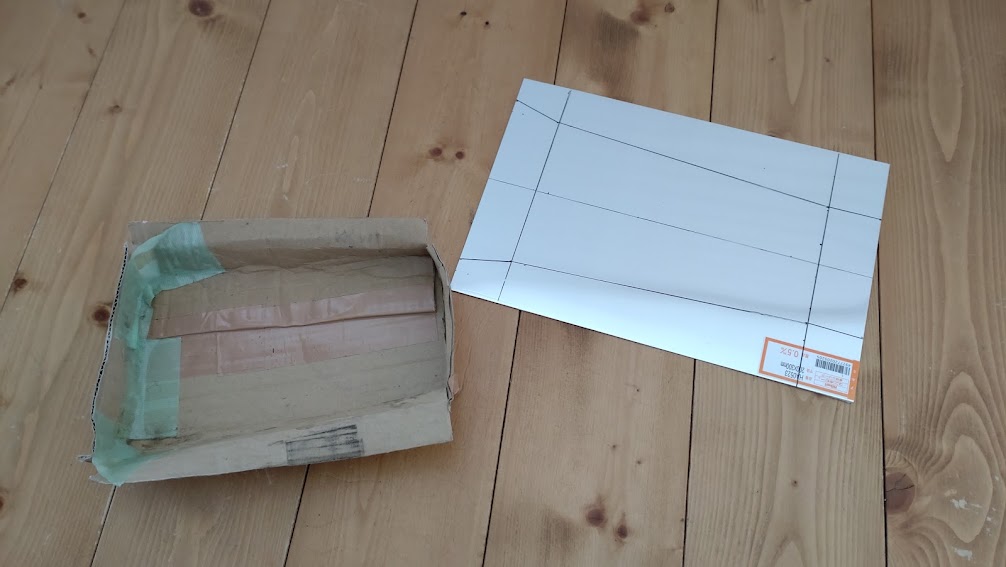
切り取り線、折れ線を決めたら、金切りバサミなどでカットしていく。
0.5mm厚の板なので、切り口は刃物のように鋭利。
加工する時は手袋を使用して、切り口はヤスリなどでなだらかにしておく。
板を折る、曲げる時は、角材の端材などを当ててやる。
こうすることで線の通りに曲がるようになる。
0.5mm厚の柔らかい素材をハンマーなどで直接叩くと、ボコボコとなる。
必ず木を当ててから叩いてやる。
間違った時も、手で曲げると歪んでしまうので(やった人)、できるだけ木を当てながら少しずつ戻してゆく。
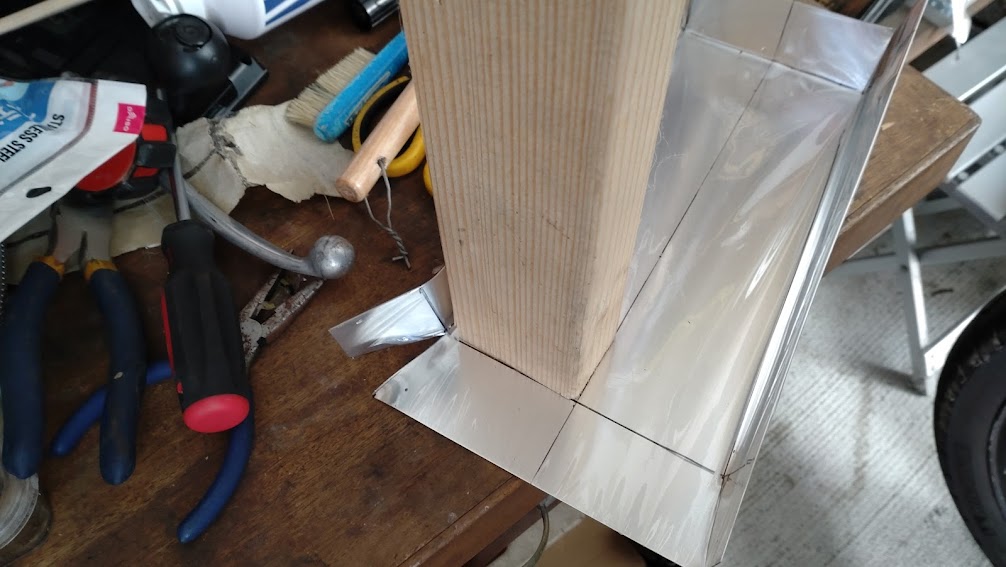
4辺をハコ型に折り曲げたら、90%は完成。
これが紙製だったらボンドで貼って終わりなのだが、金属だとそうはいかない。
基本は溶接やはんだ付け。
ただ、この厚さで溶接したら、母材(アルミの板)に穴が開いてしまうんじゃないだろうか。
いずれにせよ「高等テクニック」が要るので却下。
では、はんだ付けならどうか?アルミのはんだ付けも出来ないことはないのだが、強度の問題から一般的ではない(できるものはある)。
手持ちに材料があればいいが、これを買って作るくらいなら、もう少し材料から良いものを選びたいし、最終的には価格も数千円になってしまう…
ようするに、曲げた板が動かなくなればいいのだから、リベットのようなモノで止めればいい。
リベットも買えばそれなりにするんだろう。
ならば、と思いついたのが「ハトメ」だ。
重なった部分に穴を開けて、ハトメで止めればリベット代わりになる。
材料が0.5mm×2枚なので1mm。
布とほとんど変わらないだろう。
というわけで、ハトメパンチを購入。
ハトメの玉も買おうとしたのだが、在庫切れ…!
だが、ラッキーなことにハトメパンチに試供品の玉が入っていた。
4か所を止めるだけなので、6個もあれば十分。
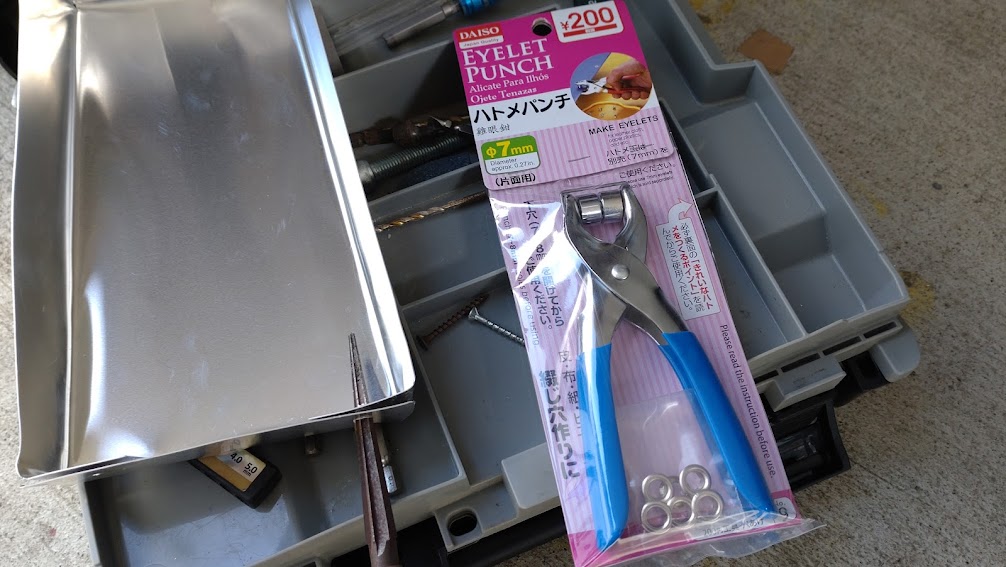
写真ではすでにリーマーを通しているけど(笑)、まずはドリルで穴を開けていく。
最終的には7mmで開けるのだが、まずは細いドリルから。
手持ちのドリルビットは6mmが最大だったので、そこから先はリーマーで広げる。
リーマー使うと、出口に切りカスがたまるので、やすりで落としてやる。
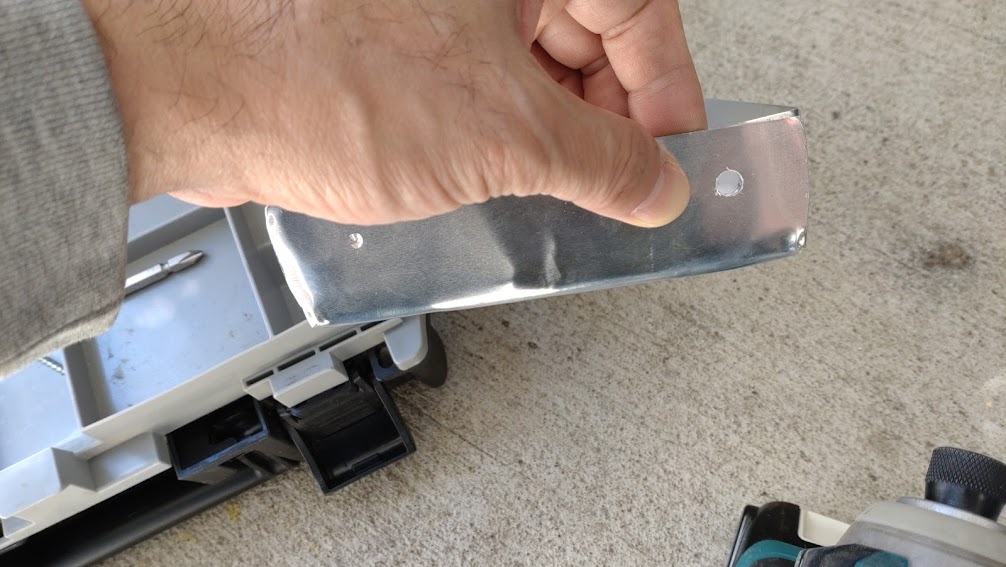
穴を開ける時は、ドリルのトルクで材料ごともっていかれないよう、出来れば万力でしっかりと固定する。
素手で持って刃を当てると、かなり危険(軍手もダメ。ドリルの刃に繊維が少しでも触れると、そのまま巻き込んで指を切ったりへし折ったりすることもある)。
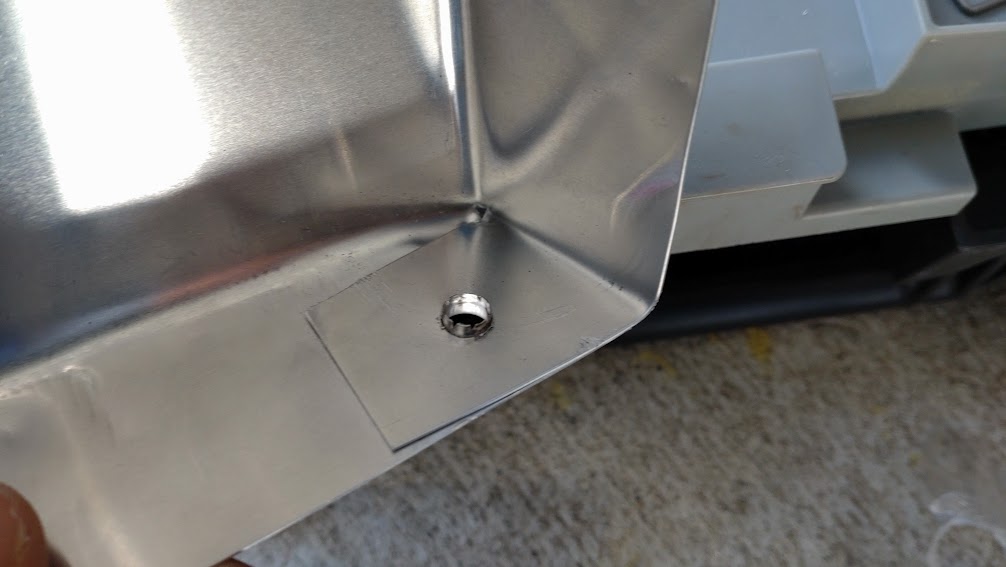
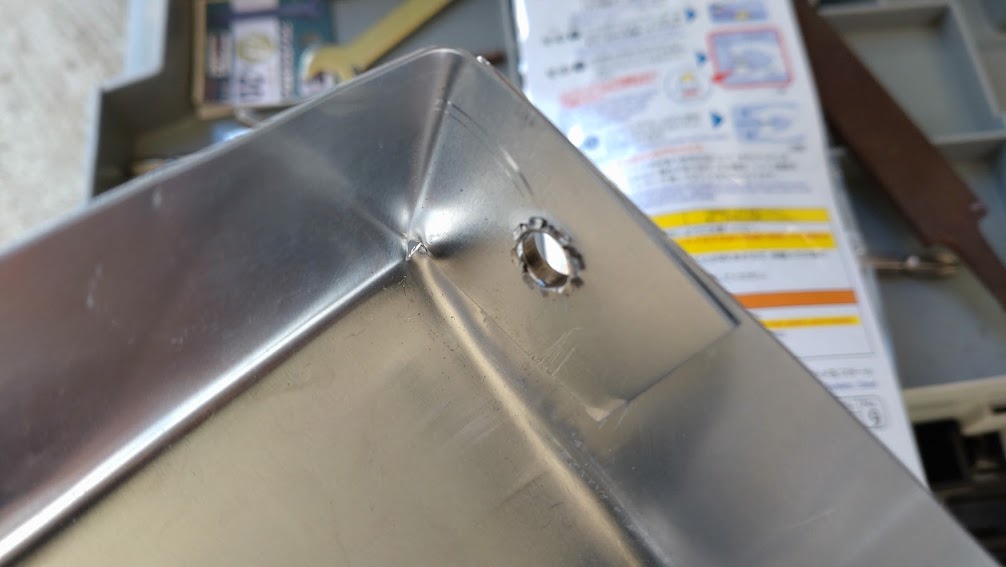
穴を開けたら、ハトメを入れてペンチで握る。
ハトメパンチは、丸い玉のようなパーツがついている方を花びら状の方に向けて握る。
玉が花びらを押し広げて、固定してくれる。
四隅に穴を開け、ハトメをつければ完成なのだが、ここで注意したいのが穴の位置。
端部から遠いところに開口するとペンチのリーチが届かず、締め込みが出来なくなる(やった人)。
こういう時はしょうがないので、ナベネジなど半球状のモノを置いてハンマーで叩く。
強すぎるとハトメが歪んだり、壊れてしまうので、ほどほどの力で。
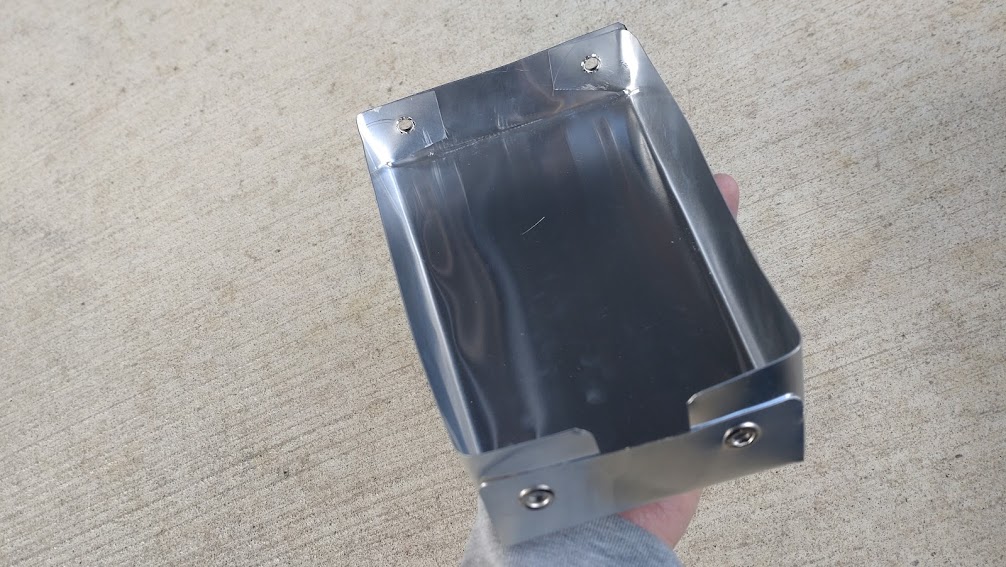
このまま使ってもいいのだが、この下に小物を入れた別の工具箱があり、触れ合うとガタガタうるさそうなので、振動防止のスポンジをつける。
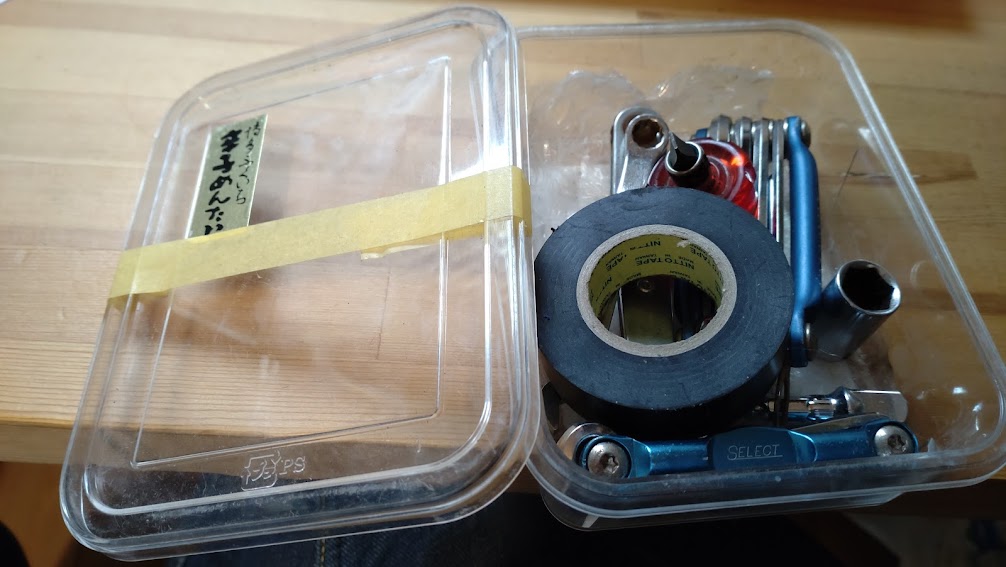
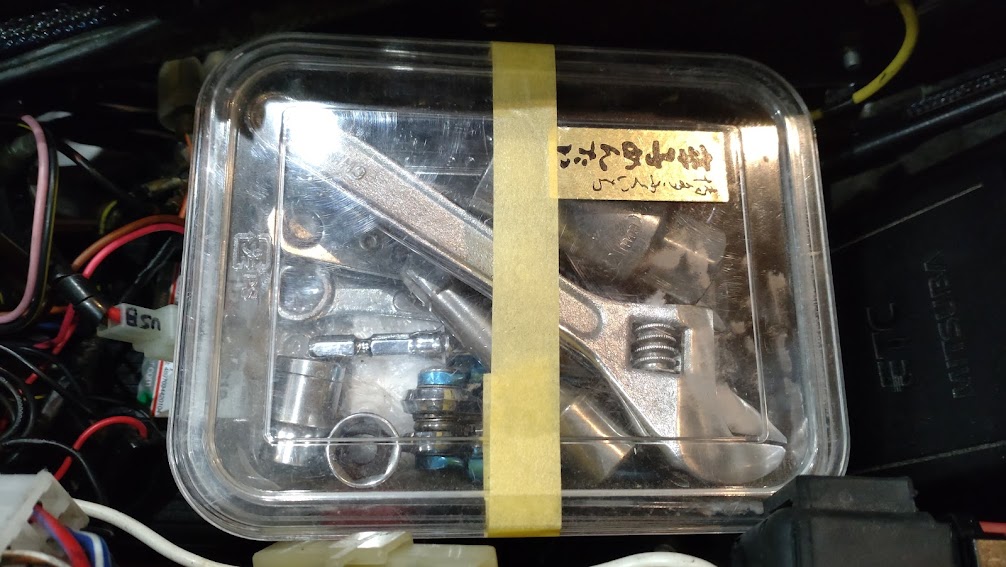
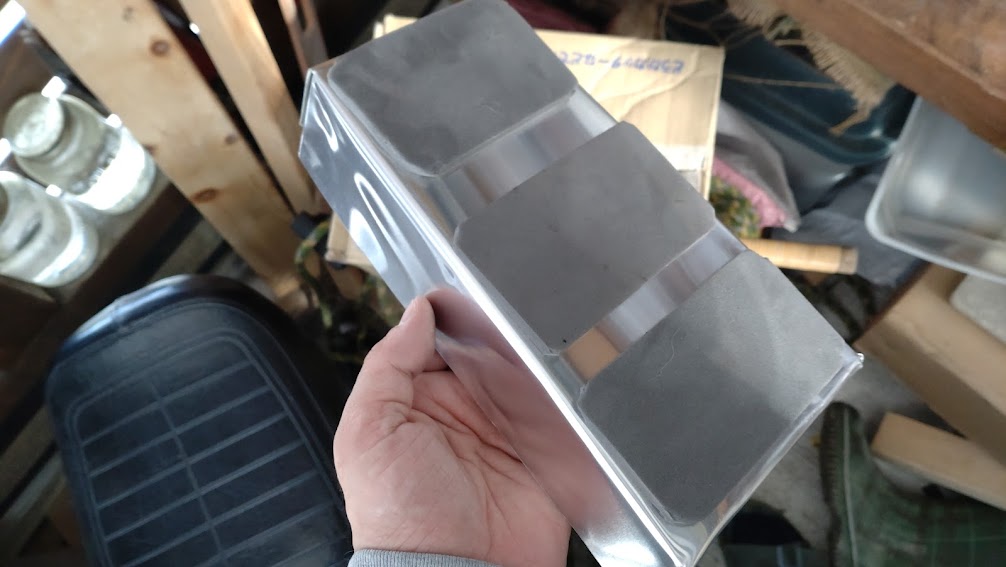
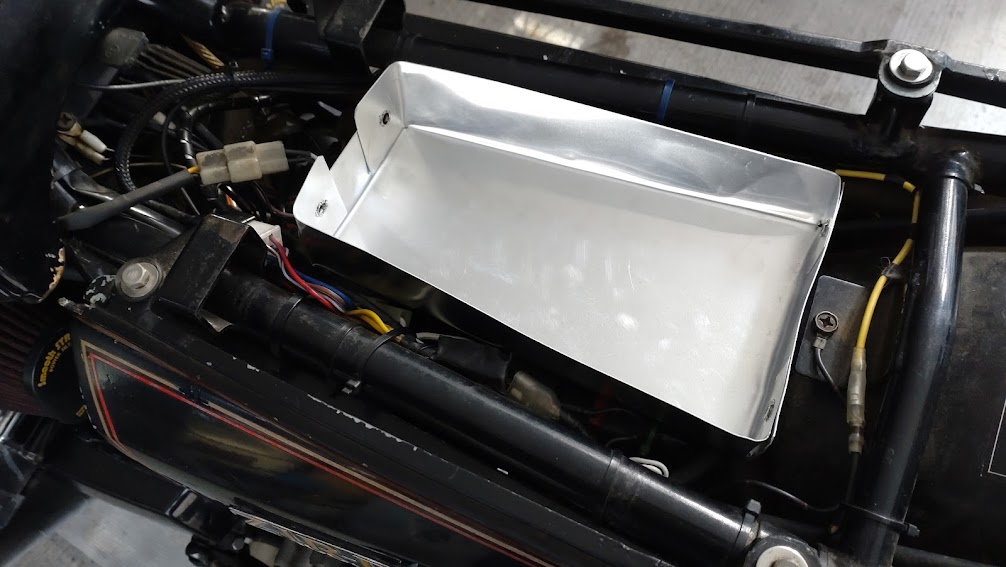
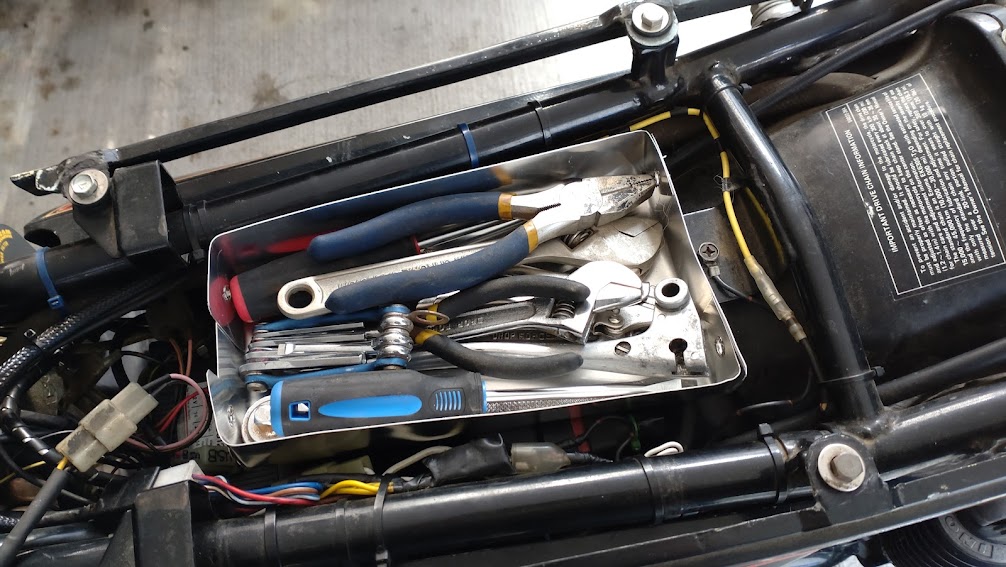
こんな感じで完成。
車載工具は非常用だけど、通常の精神状態ではない時に作業するわけだから、あまりにもクオリティが低い場合、ネジをなめたり、工具がぶっ壊れてしまうことがあるので要注意。
とかいいつつ、ここに載せている工具のほとんどがDAISOで購入したものだったりする(笑)。