梅雨入りしてバイクに乗れない日々をどう過ごすのか。
夏まですっぱりバイクから離れるのもアリだけど、これを機に普段やらないことをやるのもひとつ。
タイトルにもあるのでお気づきだろうけど、今回はいよいよ3Dプリンターで部品を造ってみることに。
みんな3Dプリンターは知ってるよね?
知らない人は、どっかで調べてから出直して!
…なんてことは言いません。
3Dプリンターくらい知ってるわい、ていう人でも、どうやって3Dプリンターにデータを入れてプリントするか、までは知らないでしょ?
ていうか、見たことすらない人の方が多数なんじゃない?
その辺も含めて、解説していこうと思います。
3Dプリンター云々言う前に、まずは何を造るかを決めないといけない。
今回造ってみたのは、Z1R乗りなら1度くらいは紛失したことがある(?)、カウルエンドキャップ。
大したものじゃないのに、買うとものすごい高いパーツ。
それに形も台形で単純だし。
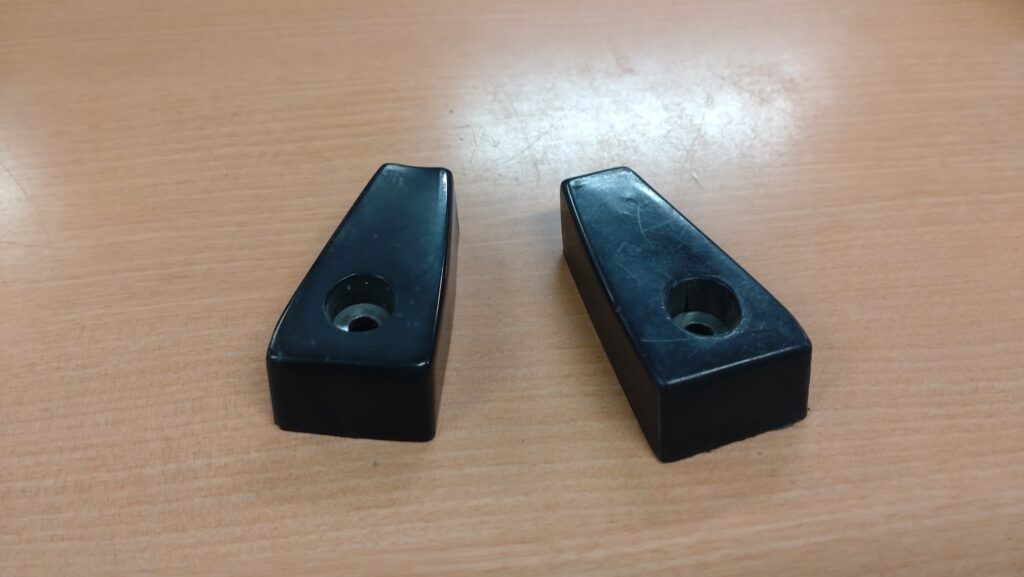
造る部品は、決まった。
次に何をするかというと、採寸。
完全コピーするんだったら、3Dスキャナというものがあるんだけど。
今回は、パーツ各部の寸法を計測して、それをデータにしていく。
まずは、こんな感じで寸法を計測していく。
正確に測りづらいところもあるけど、概算でも数値が出ないと始まらないので、とにかく何でもかんでも数字に置き換える。
カウルエンドキャップなんて単純な形なので、そんなに計測する箇所がないように見えるけど、実際やってみると案外あちこちの情報が必要になる。
最終的に使わなくなる箇所もあるかもしれないけど、測れる箇所は長さ、角度、とにかく測りまくる。
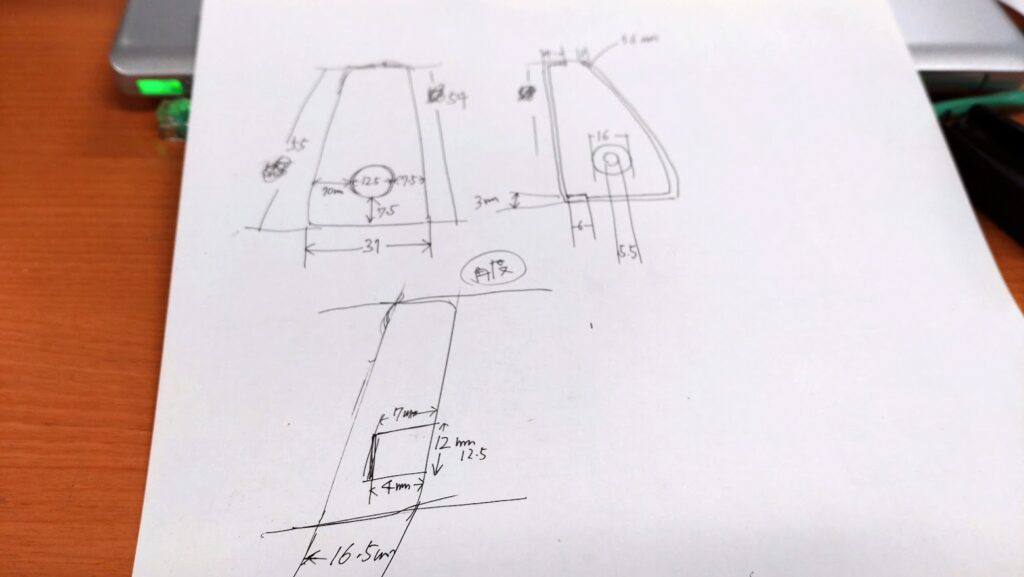
全部を計測したら、今度は3D CADソフトに図面を引いていく。
いろいろな種類があるらしいけど、今回は仕事のからみで使えることになったSolid Works というソフトを使う。
ちなみに、これ普通に買うと余裕で100万円以上する高額商品!
とてもじゃないけど趣味で買えるものじゃない。
比較的安価なソフトとしては、Fusion360というのがあります。
とはいえ、年間で7万円くらいのサブスクリプションだから、ガチで使いこなす気概は必要かも。
詳しいことについては、皆さんでググってほしい。
Solid WorksはおろかCADソフトを使ったのも生まれて初めてなんで(笑)。
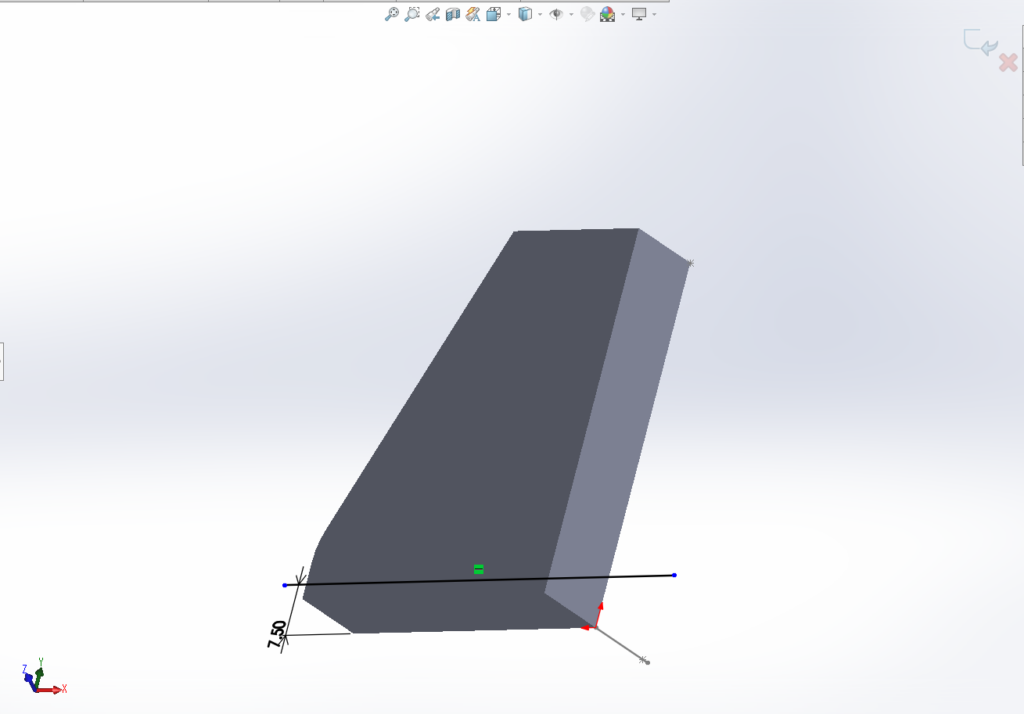
最初はこんな感じで大まかな線を引き、測った寸法を入れ込んでいく。
数値がおかしいと、見た目が全然違うものになったり、エラーが出るので分かりやすい。
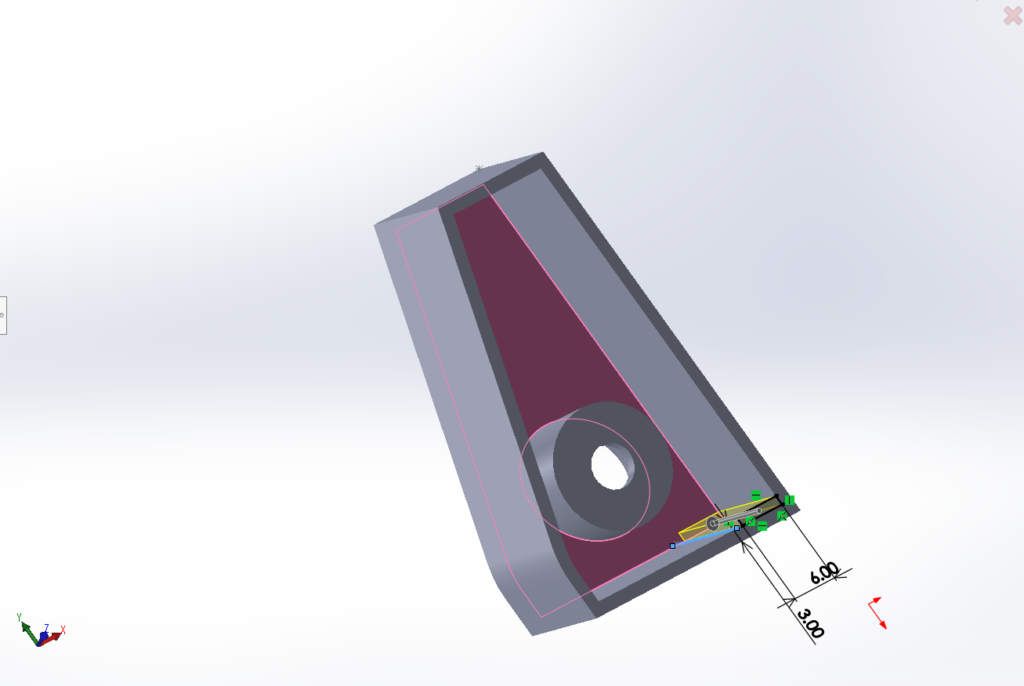
くりぬいたり、新しいパーツを足したりを繰り返して、だんだんと形にしていく。
分かりやすくするために線画にしてみたり…
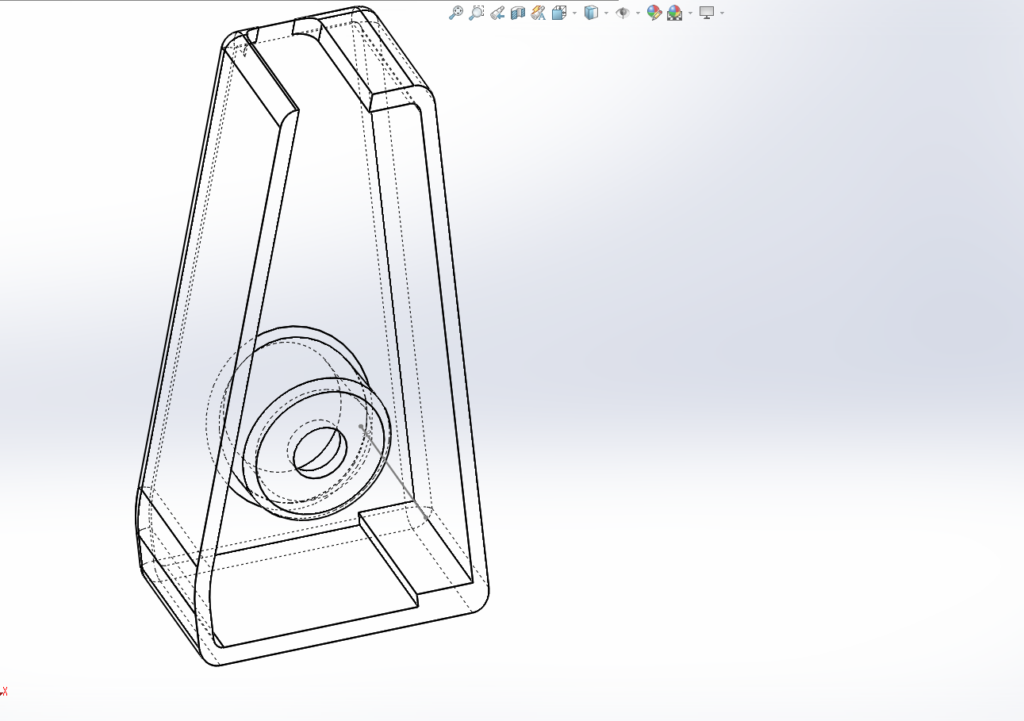
イメージをつかみたい時は、着色してやる。
マウスを操作すると、グリグリ動くので、全体的にイメージしやすい。

あとは職場にいる10年選手の達人を捕まえて、そっとカウルエンドキャップを渡します(笑)。
途中経過をかなりすっ飛ばしますが、ざっくりいうとこんな手順。
平面の形をつくる。
厚みをつける。
くりぬく。
ボルト穴用のパーツをつける。
角を取ってみたり、微調整する。
3Dプリンターにデータを転送する。
出力。
完成。
こう書くと、あっという間のようにも見えるけど、設計だけでも数時間を要したという…
達人はバイクのパーツに馴染みがなく、自分は設計のせの字も分からず、という二人三脚というより二人羽織状態(笑)。
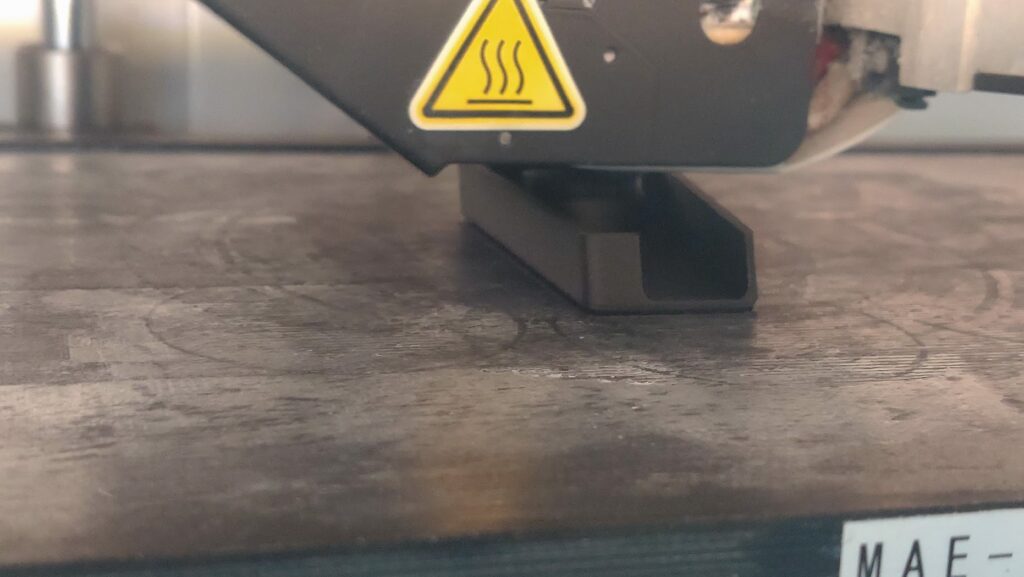
こんな風にノズルから樹脂が吹きつけられ、コンマ何ミリで樹脂が積み上げられていく。
薄紙を積み重ねていくような作業なので、こんな小さなパーツでも完成まで1時間以上を要する。
1個しか作っていないのは、画面と現物がどれくらい一致するか調べるため。
なので、最初の2回は形状や質感などをチェックするだけで終わった。
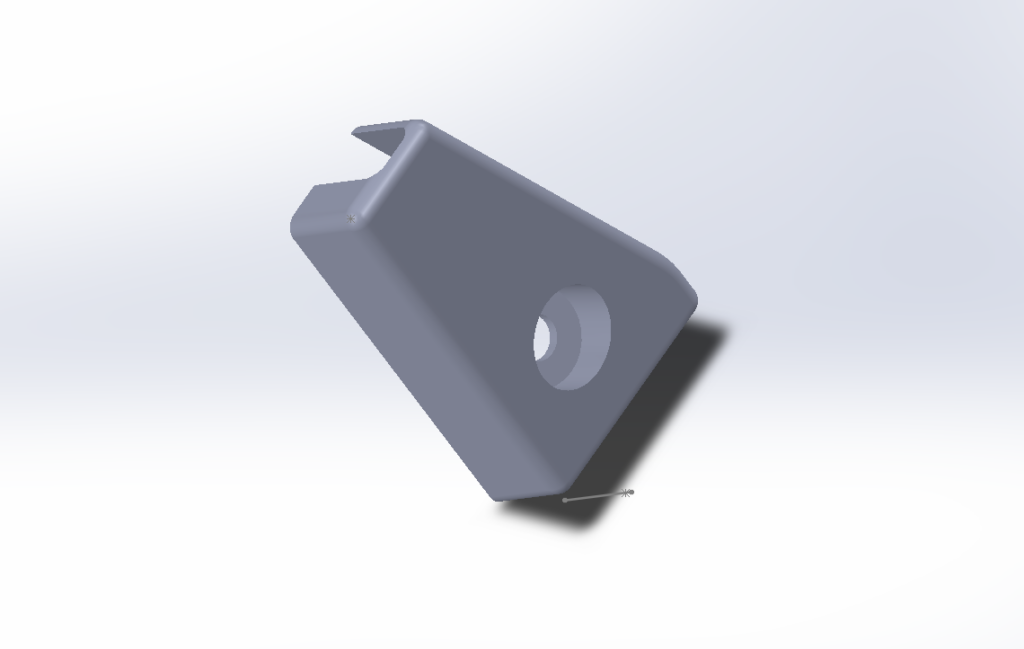
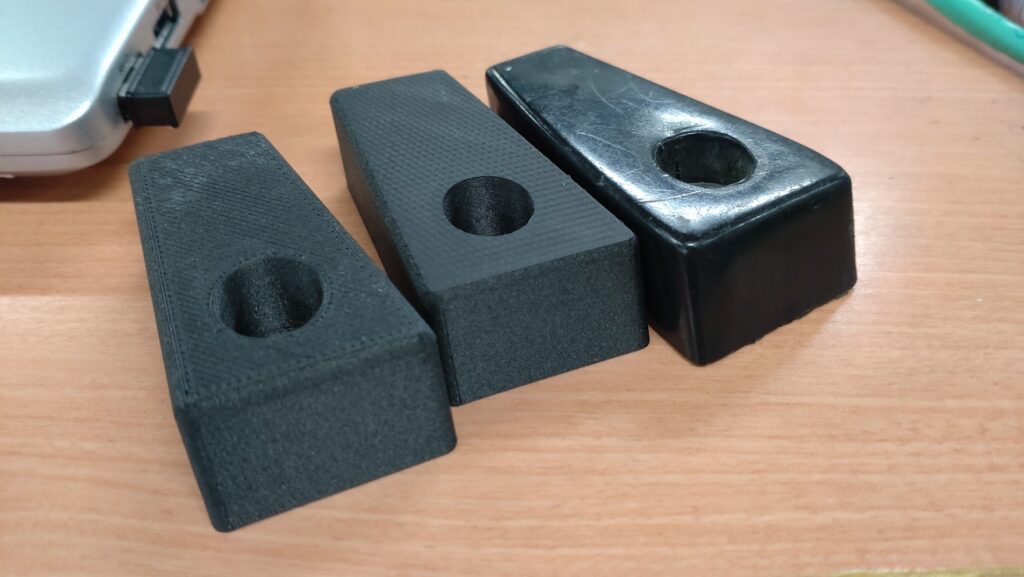
Solid Works上では角を取ったつもりが、プリントしてみると角が強く残っている。
こうして現物にどんどん近づけていく。
解釈に自信がついたら、いよいよ左右同時にプリント。
ちなみに3D CADの良いところが、鏡に映ったようにコピーできるので、コマンドひとつで反対側の図面が出来上がる。
修正を重ねた3回目、いよいよ左右のパーツを出力して実機に取り付けてみる。
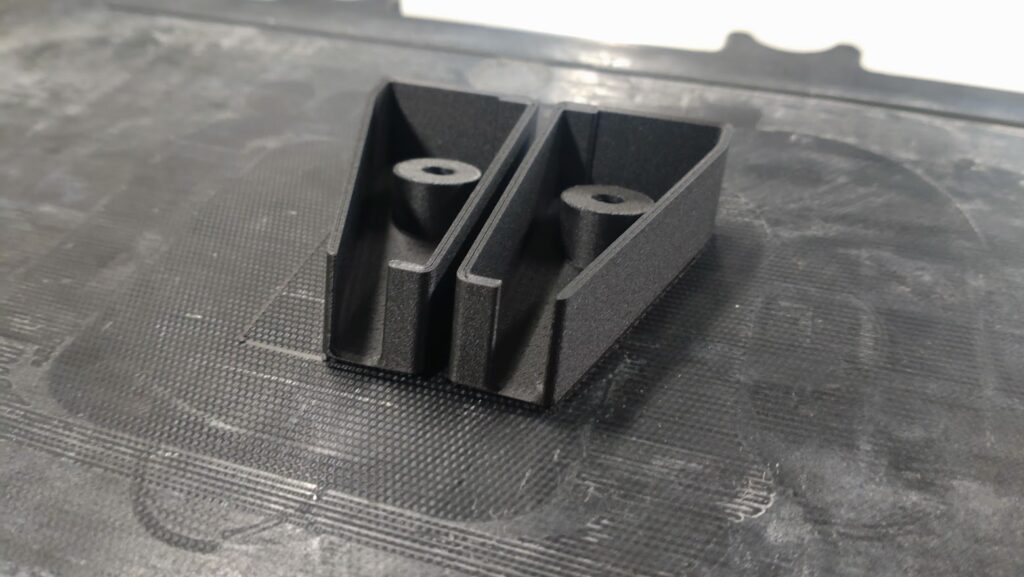
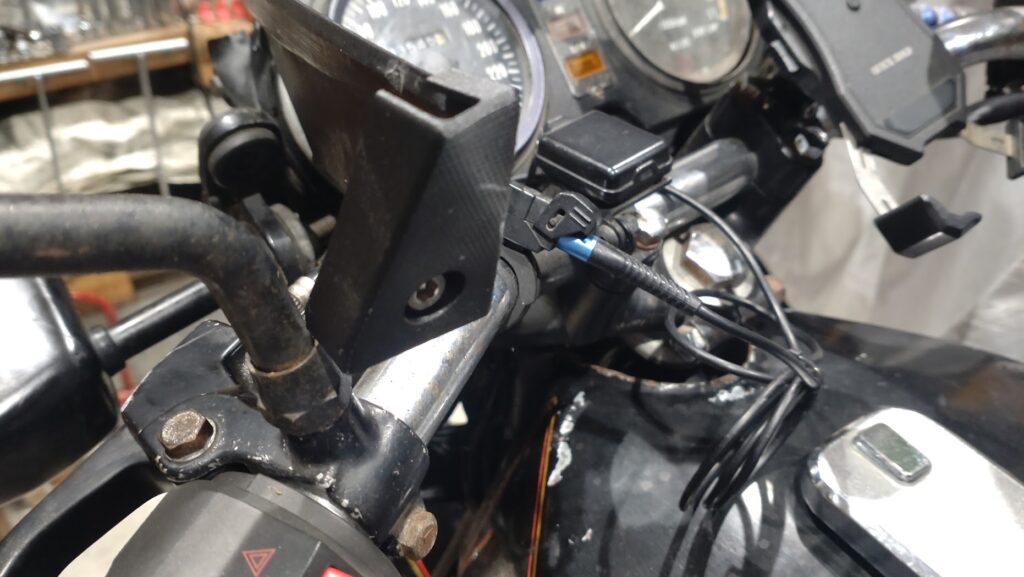
実際に取り付けてみたところ。
ボルト穴の出口の角度が現物と違っていて、クリアランスが大きくなってしまった。
そして、切り欠きの位置も若干ズレている。
あと、実はカウルエンドキャップは台形のように見えて台形じゃない。
辺の途中でRを描いている部分がある。
並べてみると、一目瞭然。
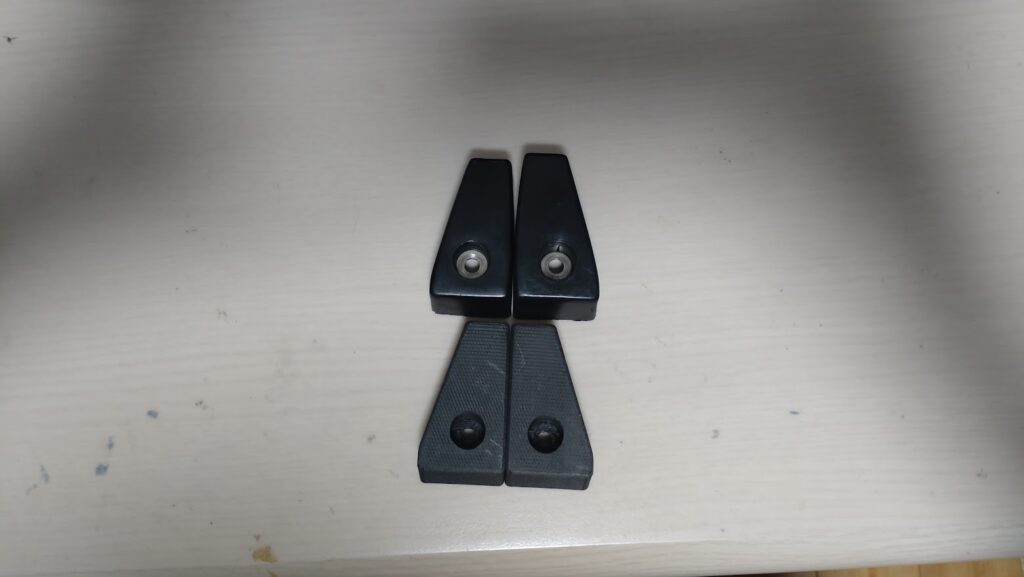
で、Rというか頂点をつけて外側に追い込んだラインを造って。
これで完成かと思ったら、追い込んだ時にSolid Worksのデータからフェアリングが収まる部分の切り欠き寸法が変わったり、トライ&エラーの繰り返し。
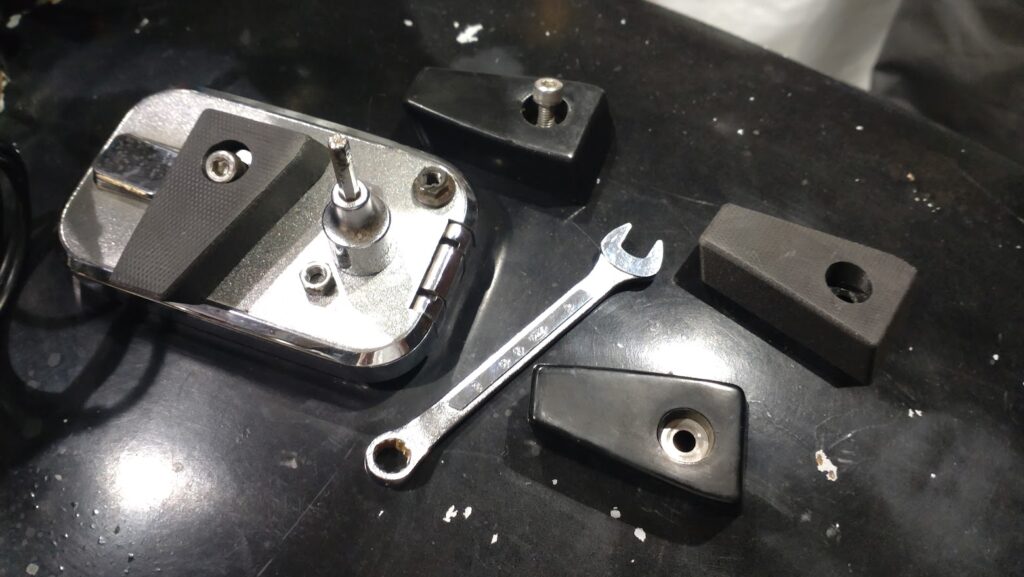
そして、4回目の出力で出来上がったのがコレ。
オリジナルを忠実に再現しつつ、フェアリングが収まる切り欠き部分を少し狭くしたのは、よりフィットさせるため。
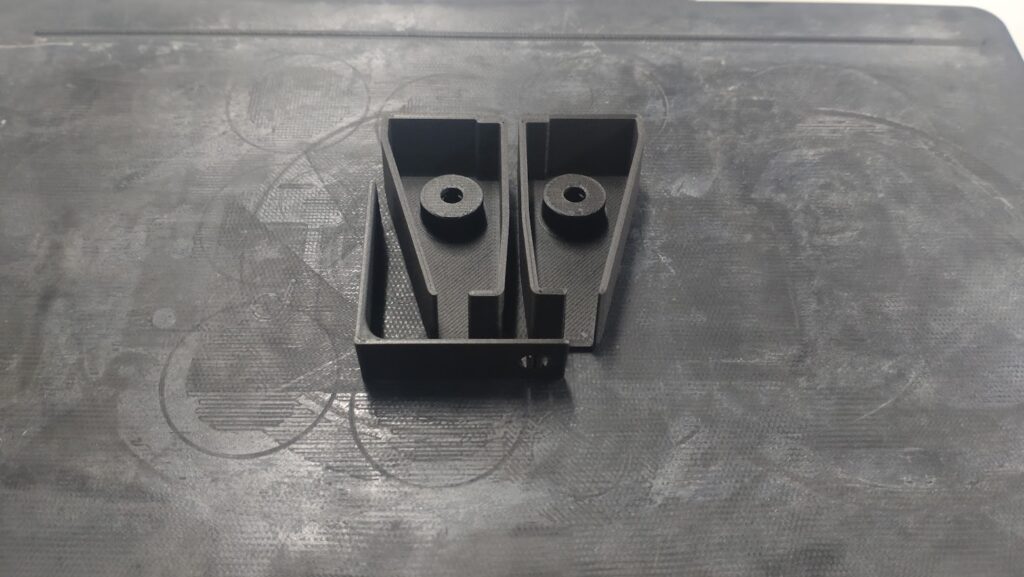
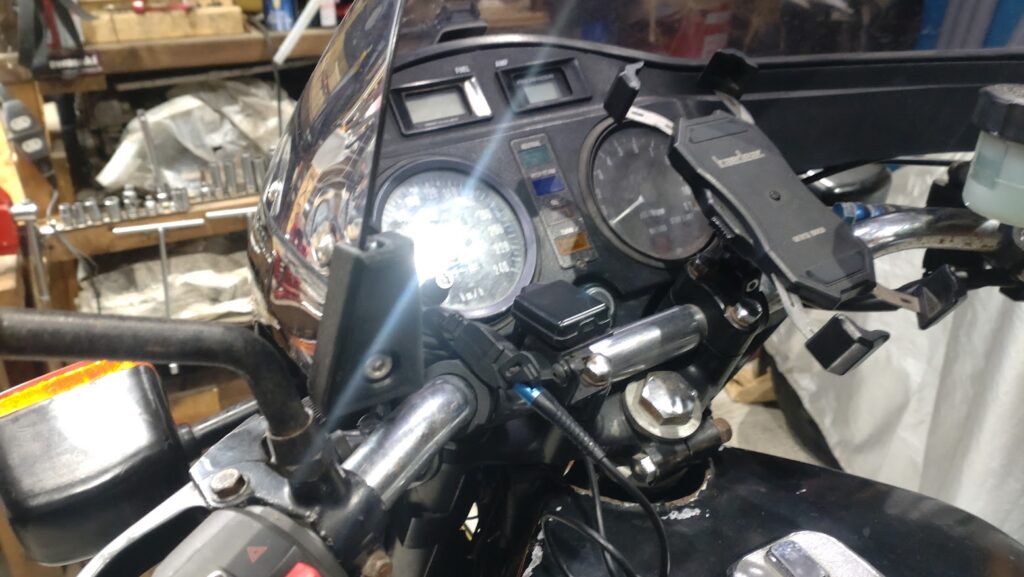
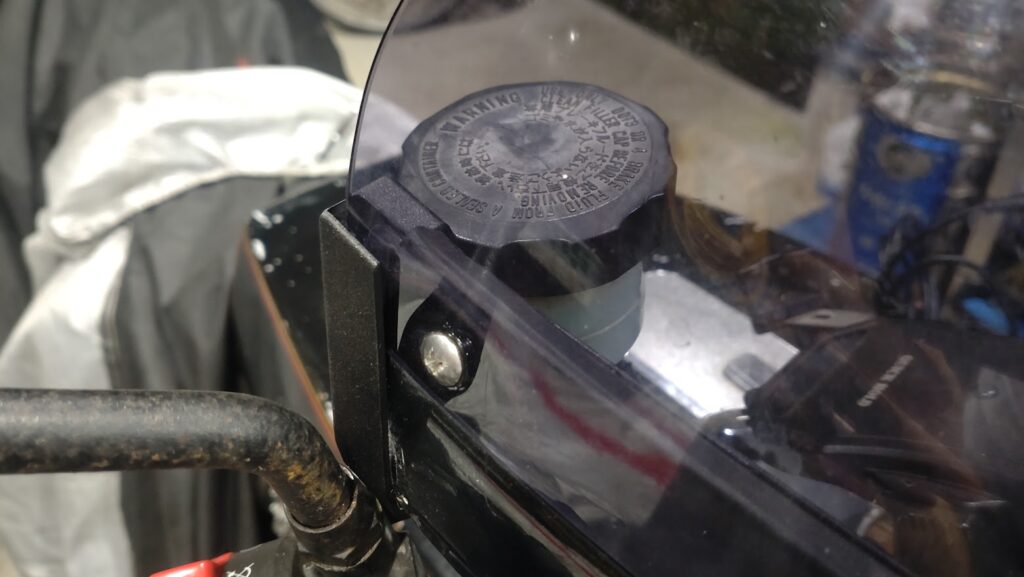
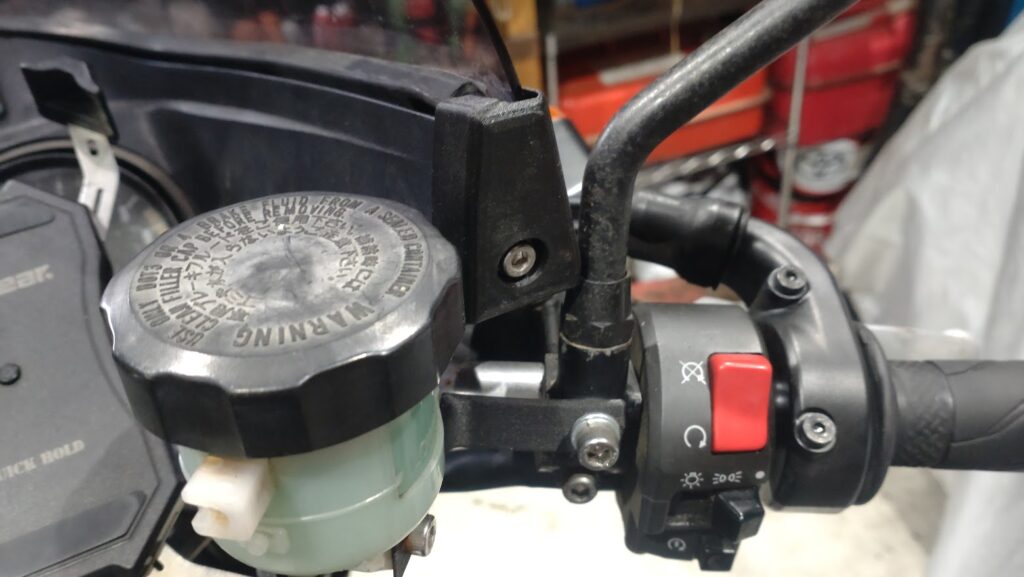
いいんじゃないでしょうか!?
オリジナルと質感や形状が微妙に違うけど、謎めいていい感じ。
よもやこれが3Dプリンターから出力されたものだと気づく人はいないだろう。
もう一点、つくったのがFブレーキのリザーバータンクを固定するブラケットというかステーというか、L字のアングル。
これはもう簡単で、一筆書きで厚みのあるL字アングルの断面図を描き、それに厚みをつけ、ボルト用の穴を開口。
角を取って、折れ曲がってるところに少し厚みを持たせた。
ついでにKawasakiの文字を浮き彫りにしてアクセントに。
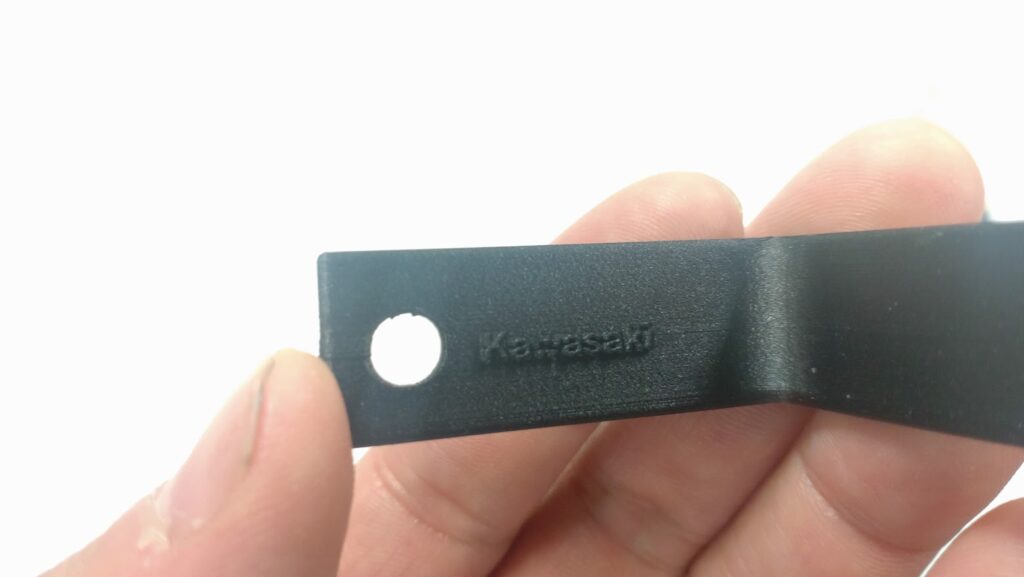
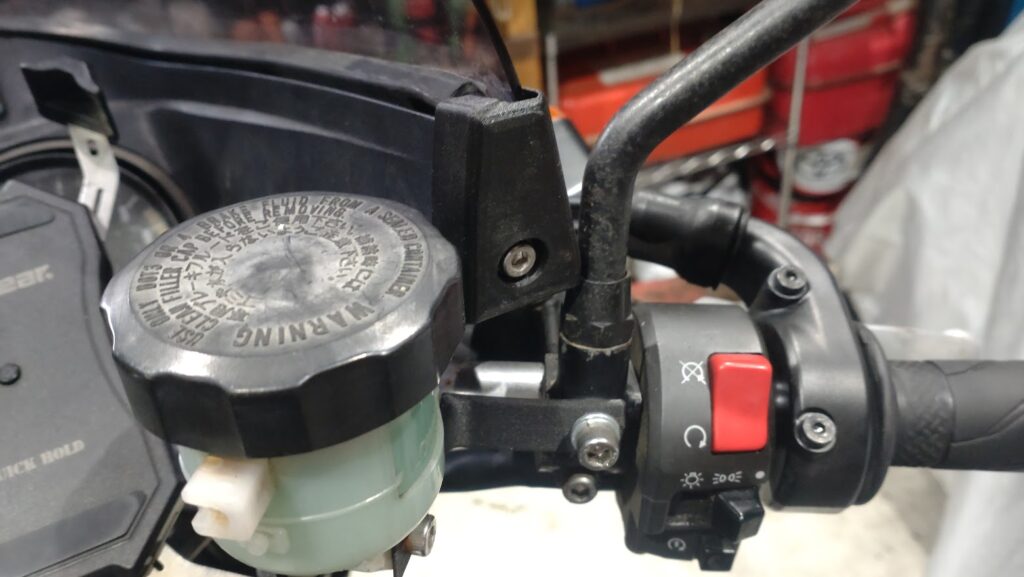
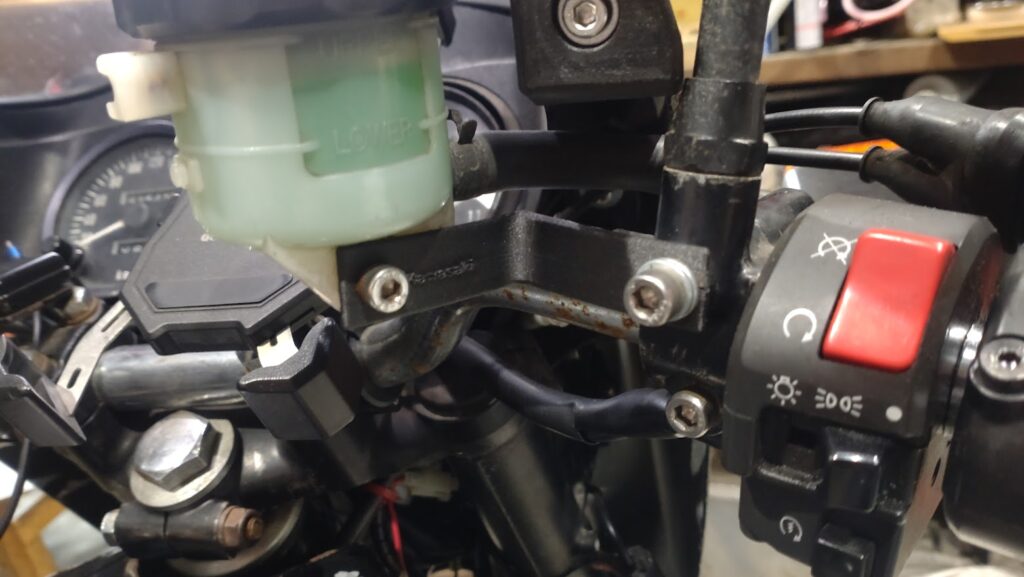
多分、手慣れた人なら10分以下で造れる。
3Dプリンターでも30分くらいじゃなかろうか?
樹脂製パーツで、極端に強度を必要としない部分は、こんな風にして作れるので良い時代になった。
ちなみに、3Dプリンターは金属を出力するものもあり、そちらではエンジンのシリンダーやエキパイなどを造ることも可能。
普段100円ショップだのホームセンターでパーツを造っているというのに、最新テクノロジーでのパーツ製作になってしまった(笑)。
追記
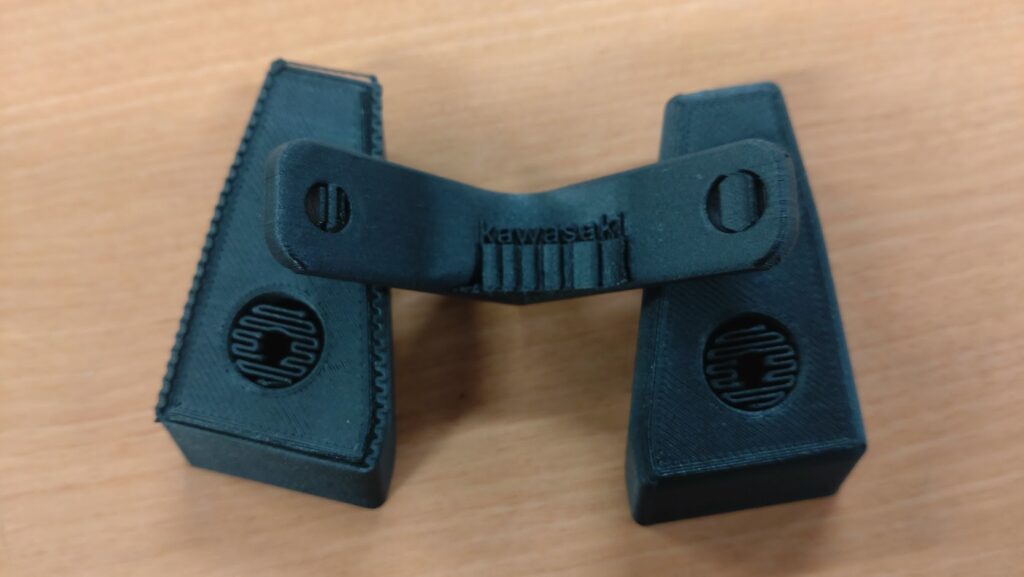
リザーバータンクを固定するL字アングル、鋼材と同じ厚みで製作したら剛性が全然弱かった。
厚みを1.6mmから3.6mmに倍増、直角部分の内側を厚くRを盛ってやる。
そこにKawasakiのロゴを押し出してスタイリッシュ…のつもり。
さらに大サービスで、材料の中にカーボン繊維を混ぜて出力したから、強度は鋼材以上(笑)。
ハニカム構造で成型しているので、ある程度、厚みがないとイカンらしい。
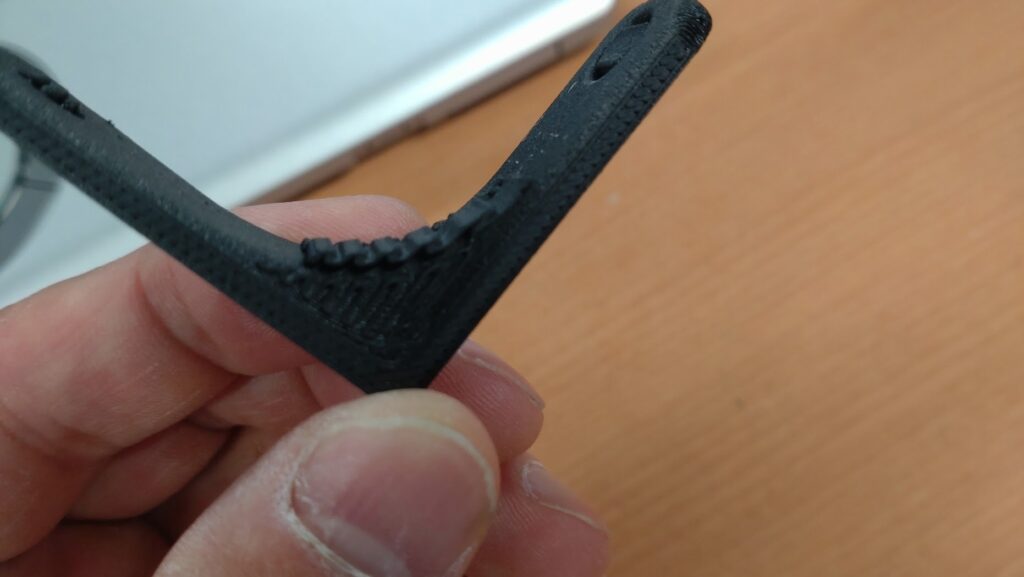
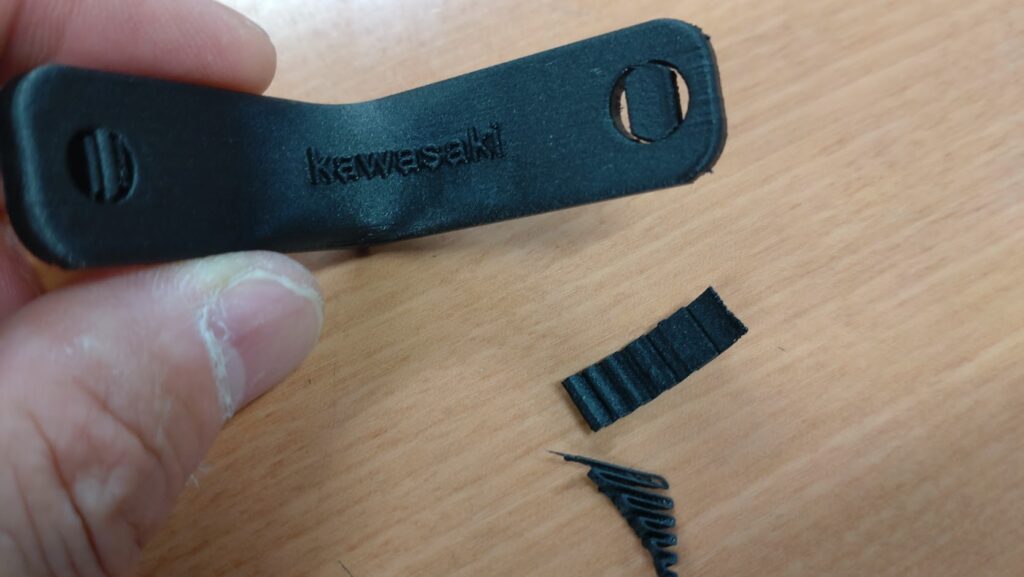
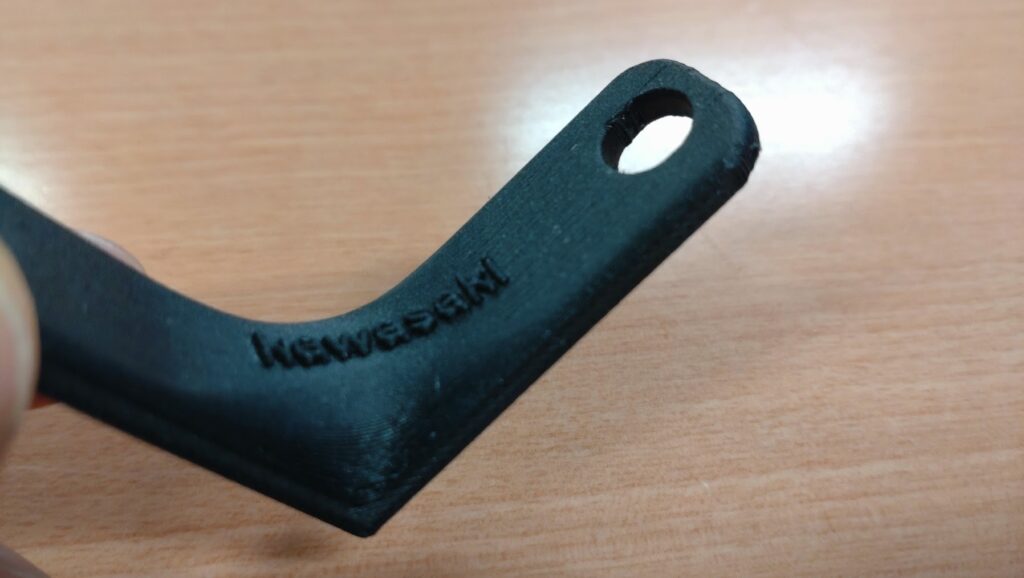
SNSにアップした時「カスみたいなのは何か」と聞かれたんだけど、これは3Dプリンターが出力する時に発生するサポート材。
3Dプリンターは自在に動くノズルが樹脂を少しずつ吹き付けるわけだが、形状によっては下がないものもある。
たとえば「L」という文字は、下から樹脂を積層していくと形になる。
しかし「T」の場合、上の「ー」状の部分は、空中に浮いているので、吹き付けると下に落ちてしまう。
なので、先に足場のようなパーツを成型して「ー」の部分を吹けるようにしている。
そしてカウルエンドキャップもフェアリングの部分、このクリアランスをもう少し詰められるのではないかと考え、隙間を3mmほど詰めてやった。
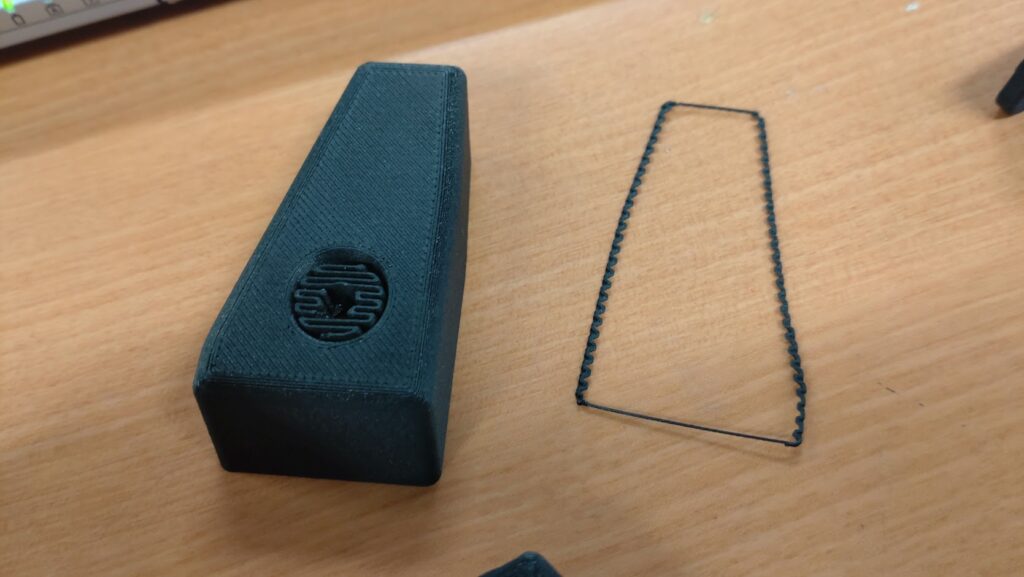
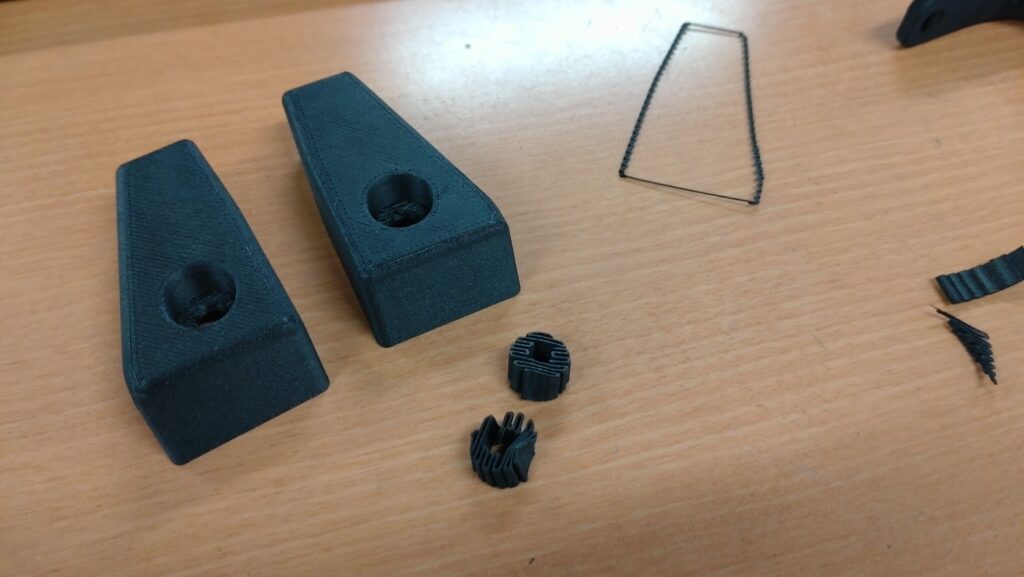
サポート材は指でペリペリはがれる場合もあるが、ボルト穴のように狭いところにしっかり成型されたモノはラジオペンチなどで無理やり引っ張り出す。
いろいろな樹脂成型の経験があると「そんなに乱暴にして大丈夫?」と思うのだが、ラフにやっても大丈夫で、むしろ思い切って引っ張った方が良いらしい。
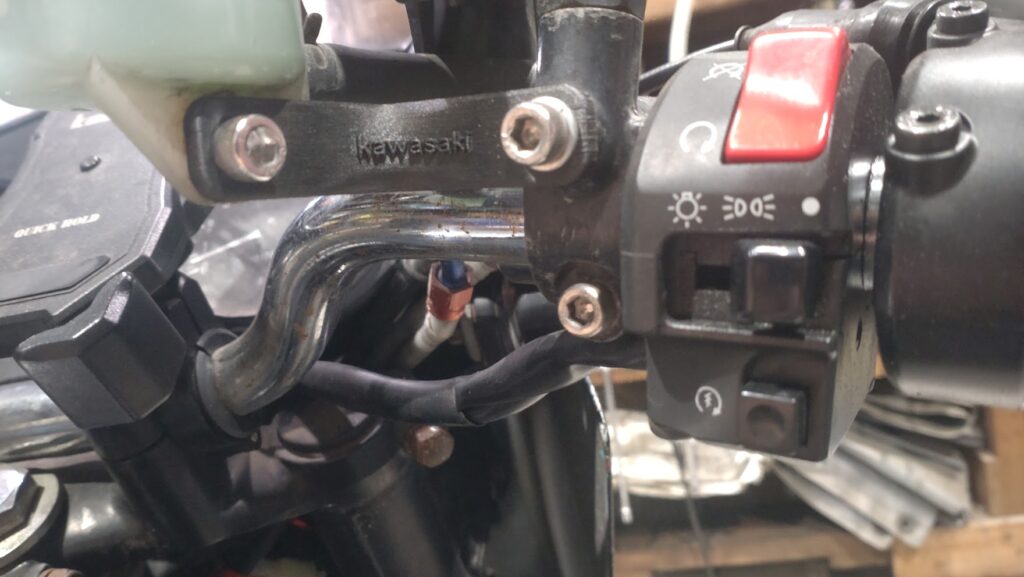
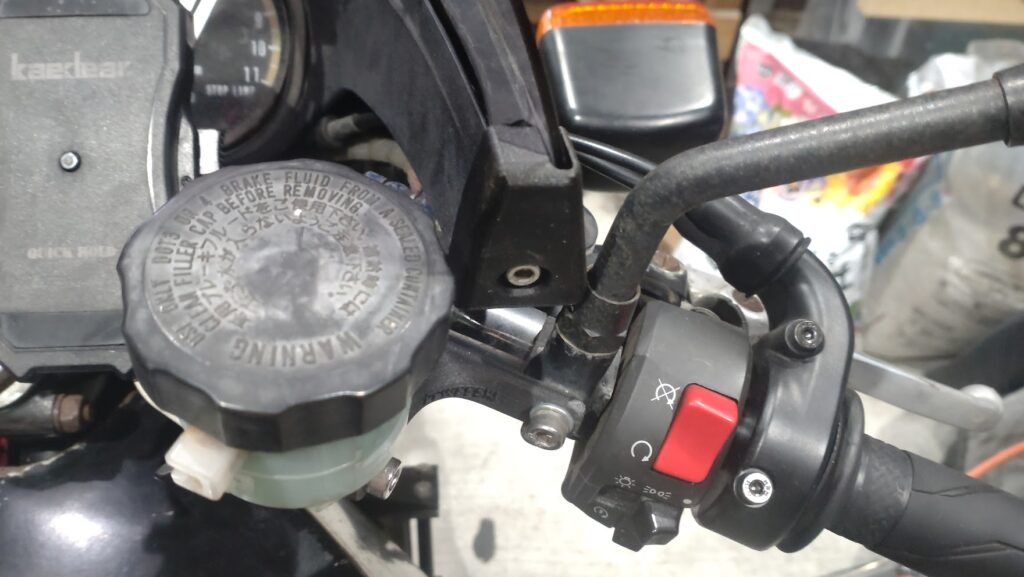
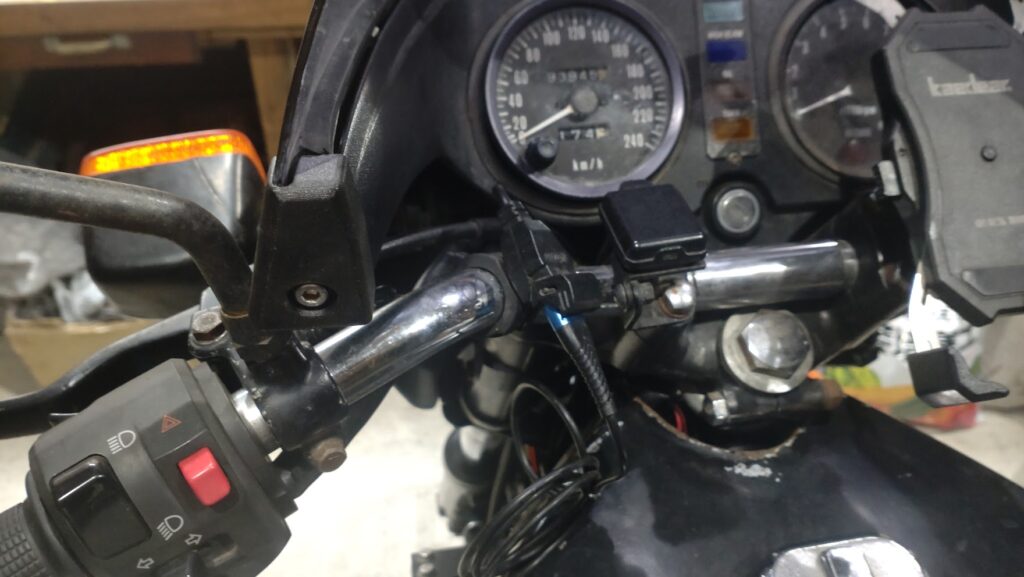
分かりますか?この絶妙なクリアランス。
ここがギリギリだと、ガタガタしなくなるというね…
オリジナルの形状とは違うかもしれないけど、これはこれで良いと思う。
おそらく3Dプリンターを使ったカスタムは、今後増えていくと思う。
カウルのような巨大な一発成型的なパーツは難しいかもしれないけど、手のひらに収まるようなパーツだったら選択肢も可能性も広がるんじゃないだろうか?