実は半年以上前に作ったもので、自分自身ではアップしていたと勘違い。
InstagramやYouTubeに投稿していたせい?
嫌ですね、年を取ると記憶もあやふやになって。
では、気を取り直して…
タイトルにある通り、またも3Dプリンターによる作例。
以前、100円ショップでも手に入るような材料で作ってみたんだけど、本体の素材が薄いせいか、だんだんと歪んできたという…
かといって、これより厚い素材にすると、ハンドツール(キッチンばさみともいう)では加工しきれない。
そもそも同じプロセスで製作するのが良いのかも分からない。
いずれにせよ、容易には作れないと思う。
少しやりくりすれば、お父っつあん、おっかさんたちでも揃えられる工具や材料でDIY製作できる作例にしたいので、100円ショップやホームセンターで材料を調達しているわけだし。
お金がないとか、ケチっているわけではないからね…多分。
とはいえ、チープ…いやコンペティティブな素材で作ったが故に耐用年数が短いものもある。
缶スプレーでの塗装と粉体塗装とでは、もちが全然違うのと同じように。
以前製作した車載工具入れも、使っているうちに歪んできてしまった。
まあ、仕方ないですね。
ペラペラの金属板だったので。
もう一度作り直すにしても、単に厚みを増やしただけでは面白くない。
あまり大きな声では言えないけど、数々の加工機器が身近にあるので利用しない手はない、というか、責任者からも「いろいろ遊んで使い方を覚えてね」と言われているので、カウルエンドキャップを造った時と同じく3Dプリンターを使って製作することに。
3Dプリンターの利点は、出力したいモノを設計するためのCADソフトウエアの知識は必要だが、加工技術のスキルや経験は要らない。
楽器を弾きこなすのは大変だが、演奏技術がなくてもPCとソフトウエアがあれば曲を鳴らせるのと同じことだ。
「こういうものを作りたい」
というイメージが具体的ならば、どうにかたどり着ける(はず)。
しかも、車載工具入れは単純なハコなので、四辺の長さや角度などを決めて図形を作ってやれば、あとは壁の厚みだの箱の高さ(深さ)を入力すれば、あっという間に出来てしまう。
自分はまだまだ操作が不慣れだったので作業も一進一退な感じだったけど、またも名人が手伝ってくれたので、30分もかからずに設計は終了。
自分だけで造ったら単なる箱で終了していただろうが、名人から「リブを入れたらカッコよくなるんじゃないですかね」と提案されたんで、ついでに「足もつけて」と追加してもらう(笑)。
あとは、帰り際に3Dプリンターへデータを送り込み、翌朝に様子を見に行くとご覧の通り…
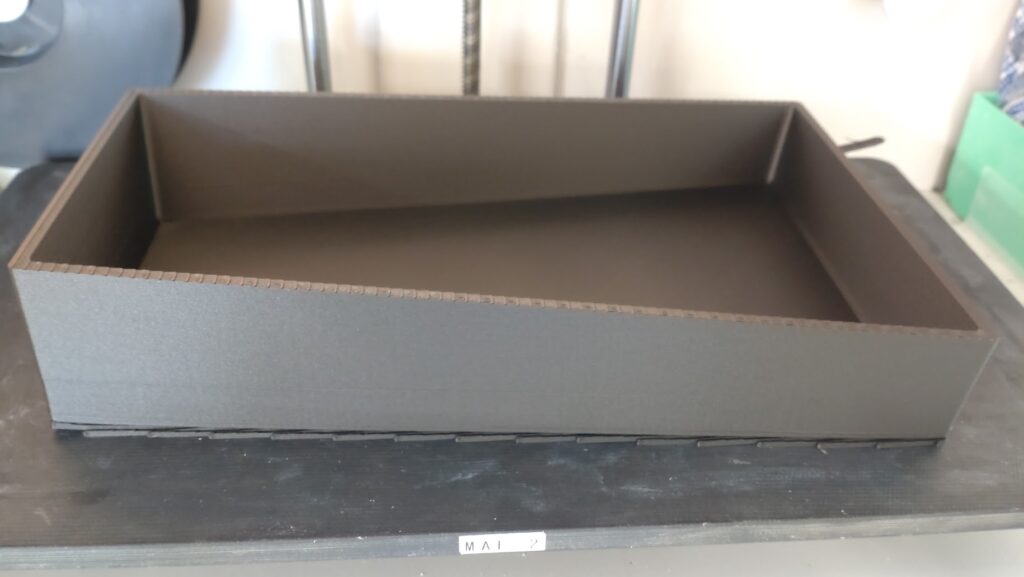
分かりづらいけど、3Dプリンターで出力が終わったところ。
黒っぽい床ごとプリンターから取り出したら、スクレーパーで剥ぎ取る。
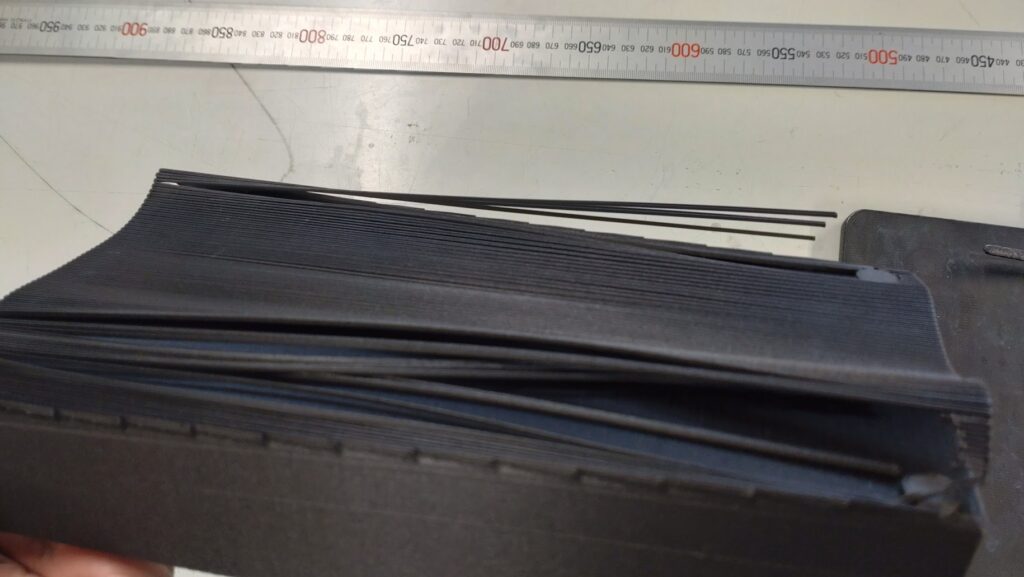
剥ぎ取ると「サポート材」がワシャワシャとくっついてくる。
サポート材とは、説明が難しいんだけど、3Dプリンターは成型する際、まな板のような台に液状の素材を少しずつ噴射して形作っていく。
紙のプリンターがヘッドを往復させて、少しずつスライドしていく紙に印刷する動き…あれが垂直になったものだと思ってくれるといいかも。
成型する物体が、横から見た時、下の層と同じか小さくなるようなもの、たとえば単純な円柱のようなものだと下から単純に重ねていけばいいんだけど、上の方が大きい形状や途中で穴が開いているようなものだと、材料を吹き付けても落下するだけになる。
そこで、足場のような部分をつくってから成型するようにしている。
今回、工具入れの底一面にサポート材がついたのは、四隅に足をつけたせいで底面が浮いているから。
もちろんサポート材はロスになるから、なるべくサポート材が少なくなるような向きで成型するのがよいのだけど、つくりたいパーツの仕上がり具合、積層構造なので木目のような「目」もあるので、そこを気にすることもある。
で、出力されたのが、こちら。
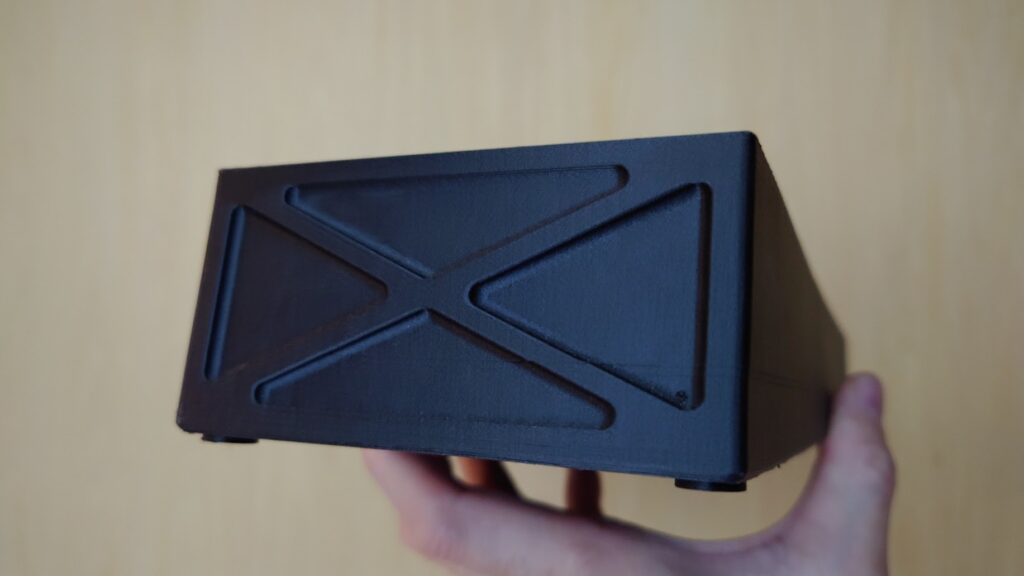
名人によるリブもついてスタイリッシュでしょ。
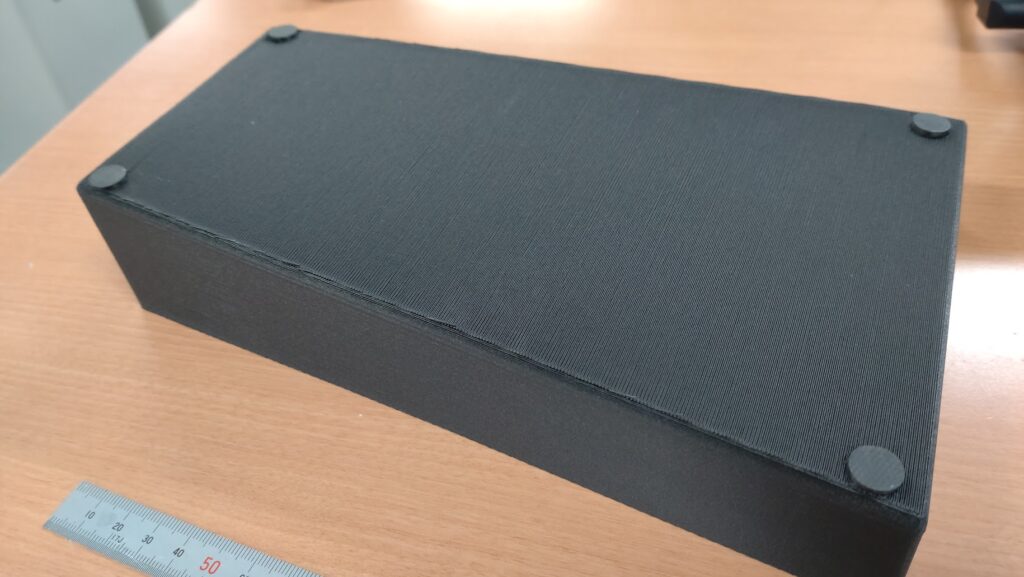
車載してしまえば見えなくなる、というのは言わない約束。
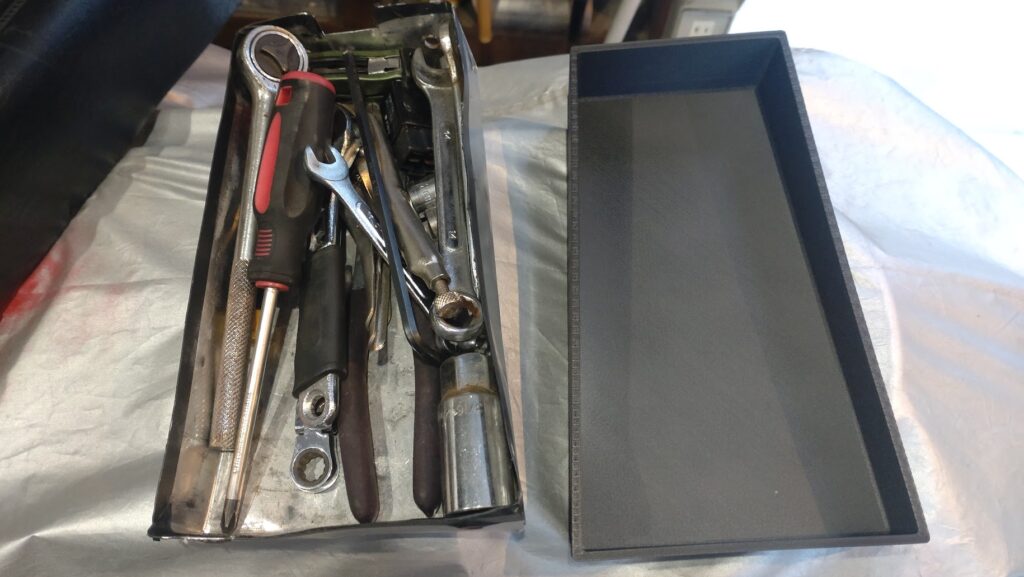
前作と比較するとこんな感じ。
台形の底辺部分を見てもらうと分かる通り、結構、歪みが出ている。
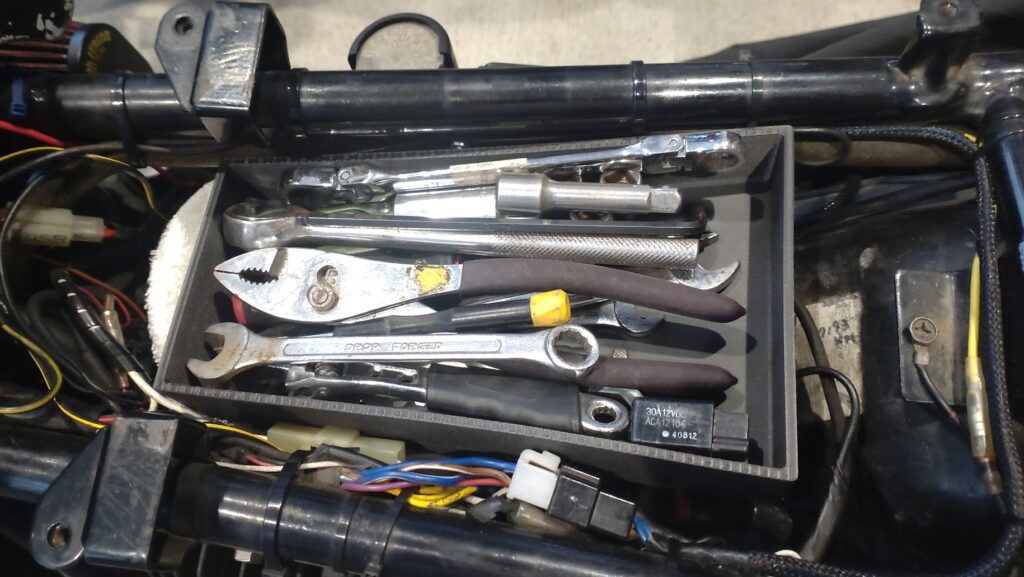
工具を入れるとこんな感じ。
フレームにぴったりと沿った形になっていないのは、我が家のZは左側に配線を逃がしているから。
もちろん、ノーマルのエアクリーナーボックスを搭載したままの車両では使用できない。
こんな感じでしばらく使っていたのだが、ある日、工具が飛び出してしまうというトラブルが。
いきつけの店に行って帰ろうとしたら「TAKEDAさん、何でエンジンの上にプライヤー置いてるの?」とか言われて(笑)。
安全上きわめてよろしくないので、急遽フタを造ることに。
これが鈑金加工だと外寸から割り出して図面を引いて…ということになるのだが、3Dプリンターだと箱のデータから簡単に造れる。
名人にやってもらったのだが、CADを立ち上げてから10分足らずで完成した。
データを3Dプリンターに送って、実際に出来上がるまでには何時間も必要とするが、紙のプリンターと同じで出力プロセスに入れば、ただ待っているだけ。
当初は本体のフチにぴったりと納まり、ヒンジで開閉する機構をつける案もあったけど、本体を包むようにして納まる単純なフタにした。
可動部をつけると脆弱性も増すし、キャパ以上の物を入れて締まらない、なんてこともある。
だったら、多少あそびがある方がいいでしょう、と。
出来上がったのがこちら。
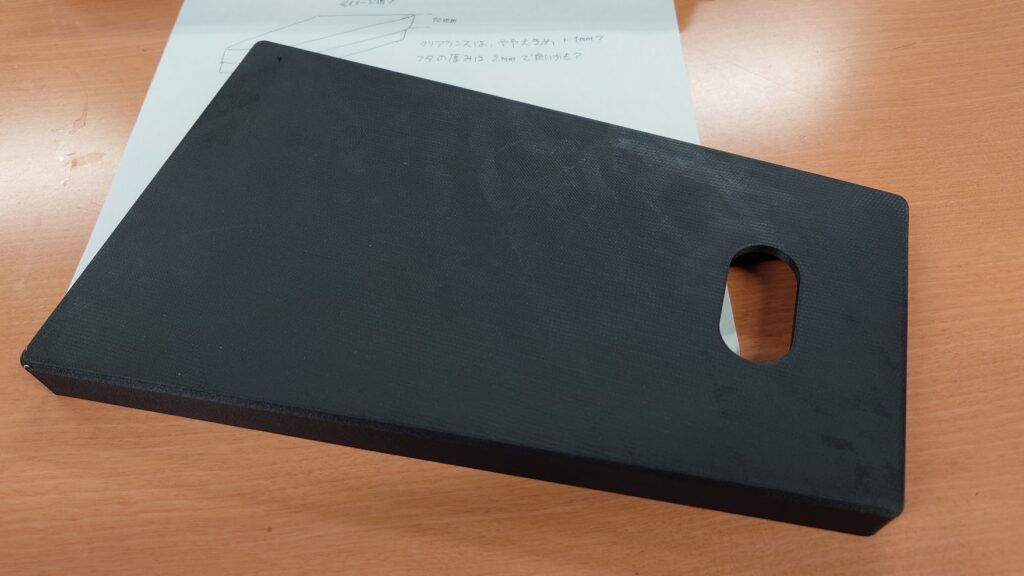
フタを開けるための「指孔」もつけてもらった。
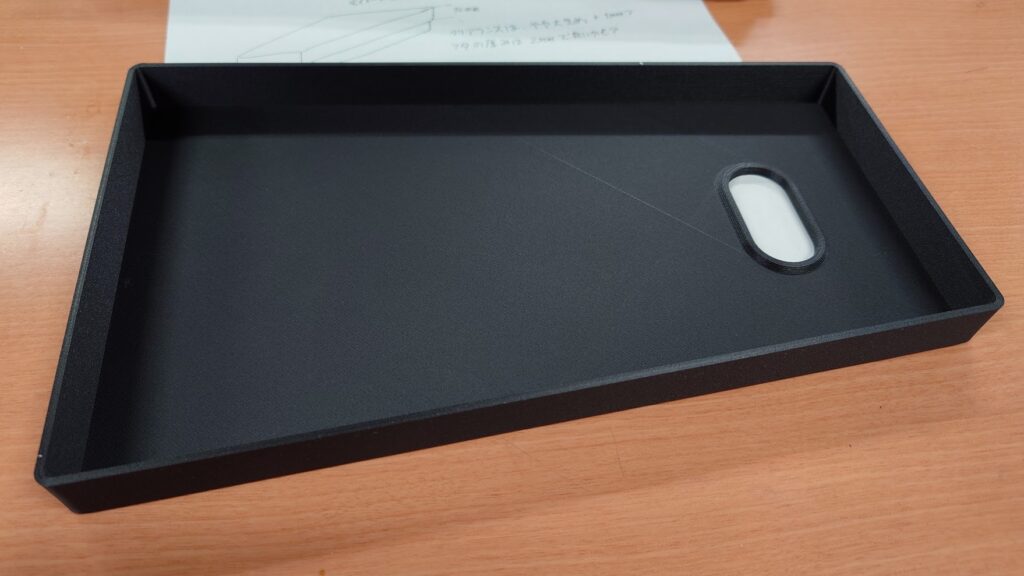
もちろん、名人ならではのこだわりもあり、本体とフタの隙間(クリアランス)の設定とか、指孔の周囲にさりげない加工も…
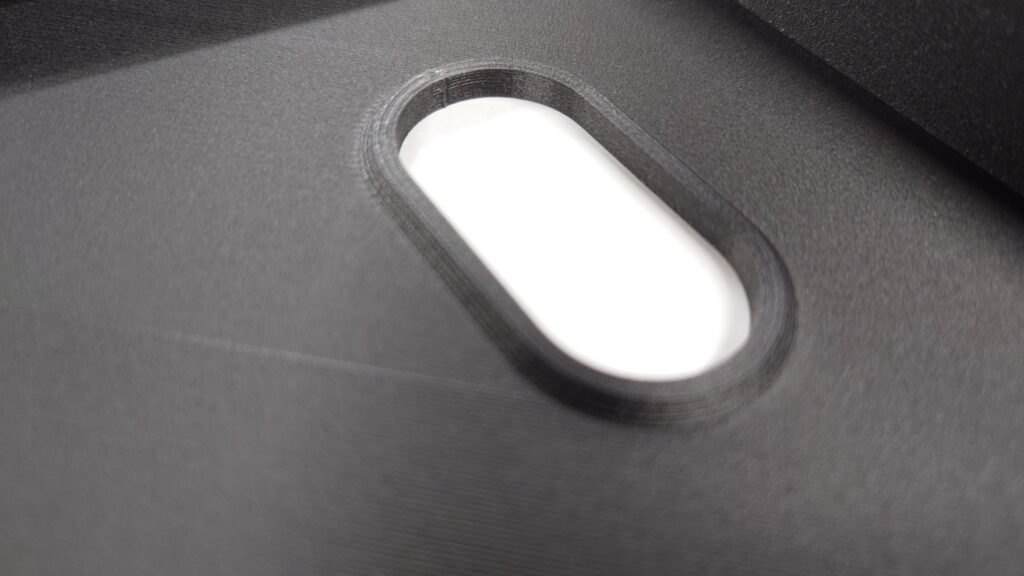
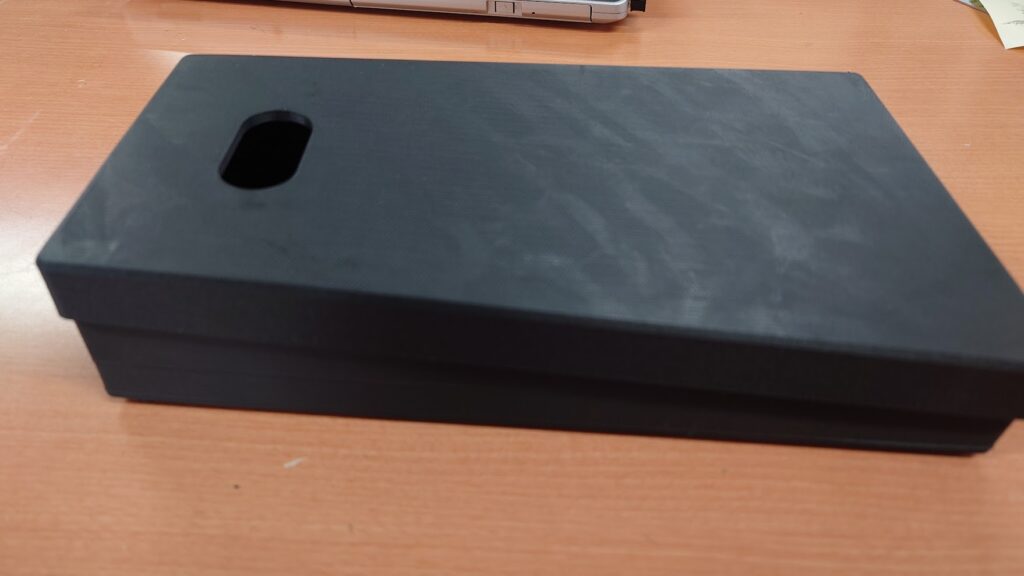
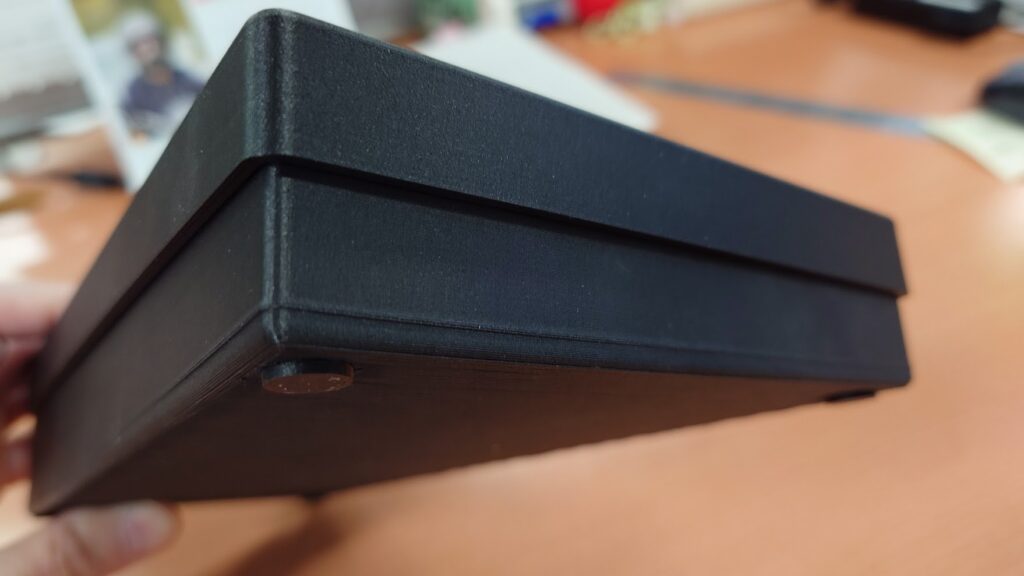
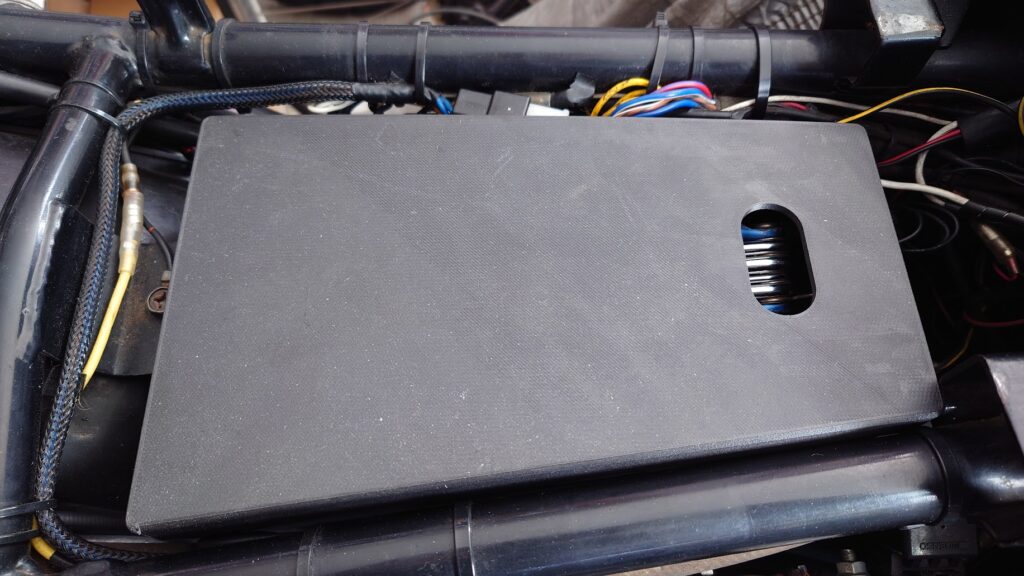
こんな感じでピッタリおさまりました…!
CADを自由自在に操れる人なら、寝る前の30分で設計して、おやすみ前にプリンターにデータをアップしたら、朝になったら出来上がり、ということも難しくないだろう。
「そんなの身近にCADと3Dプリンターがないと出来ないじゃん!」
と言われるかもしれないが、3D CADは無料利用できるモノもある。
高価な3Dプリンターを持っていなくても、データを送れば出力してくれるサービスもある。
ポスターをつくって印刷会社に頼むのと同じ感覚だ。
「コレくらいのモノなら鈑金の方が手っ取り早くね?」
たしかに、腕に覚えのある人なら、単純なハコだし、数時間で造れるかもしれない。
けど、鈑金加工技術は理屈を知っていても一朝一夕で身につくものじゃない。
道具そろえて、練習用の材料を用意して、金床の上でハンマー叩く…なんてことを頭の中で想像してごらんなさいよ。
だったらプロに頼んだ方がいいよね、という話になるでしょ?
CADも操作を覚える必要はあるけど、理解さえすれば、何かしら造れるようになる。
やり方が分からなければ、マニュアルなり書籍なり誰かにレクチャーしてもらえば、その瞬間、名人と同じことができるようになるのだからスゴい。
これまでサンメカが何かしらカスタムパーツを自分で製作する場合、純正または流用部品や素材を切った貼ったして製作するのが常だったから、具現化が難しかったりしたけど、3Dプリンターが身近なものになり、素材も樹脂だけではなく金属まで使えるようになったから(まだ高いけど)、選択肢は相当広がったと思う。
名人に手伝ってもらいながらだったが、いくつかパーツを製作してみて、非常に強く感じた。
3Dプリンターだけに、もっと知識を「積み上げて」、また新しいパーツ造りにチャレンジしたい。